- Ensure Safety program drives goal of zero injuries
- Develop and implement Manufacturing Engineering business plan focused on continuous improvement, productivity, maximizing CAPEX, TPM, and innovation
- Identify resource needs and execute staffing plan
- Utilize strategic thinking and leadership development tools
- Work cross functionally to understand business needs
- Ensure use of performance management, development plans and continuous feedback to develop team
- Achieve exceptional leadership team and solid bench strength.
- Drive regular use of GEMBA, Stage Gate and Kaizens, "walk the talk" by participating in kaizens and pushing use of SBS tools
- Develop into strategic business partner for VP Operations
- Utilize consistent communication and transparency to gain the trust of employees and motivate Manufacturing team to achieve long term growth and financial success
- Achieve success from the company and customer's perspectives
- Track record of delivering results in Manufacturing Engineering capacity
- Success utilizing strategic planning tools including metrics and countermeasures
- Demonstrated application of lean principles to achieve operations excellence
- Ability to use Manufacturing Engineering strategies, including 3D design, drawings, proof-of-concept, design for Manufacturability, material selection, component sourcing, feasibility analysis and product costing to achieve advancements in process and capability
- Successful leadership development with specific examples of mentoring and coaching direct reports
- Excellent communication and presentation skills, and strong level of self-awareness
- Demonstrated ability to execute plan to goals
- Experience creating or maintaining a strong culture promoting safety, respect, and integrity
- Experience increasing employee engagement with specific examples of tools utilized.
- Excellent PC skills including experience with MS Office Suite
- Bachelor's degree in relevant discipline preferred
- 8 to 12 years progressive and related business experience (Manufacturing Engineering preferred)
- Experience with brazing and related factors , including metallurgy, preferred
- Experience with tool and die design, technology and software preferred
- Ability to attend GEMBA and travel throughout production environment to oversee program implementation
- Work requires problem solving skills and ability to analyze data and make rational decisions
- Must be able to communicate with others in a manner that results in clear direction and interaction
- Work requires ability to utilize company computer equipment and software programs
- Work requires ability to understand engineering software programs utilizied by Manufacturing Engineers
- Work requires ability to understand Engineering principles to coach and mentor Engineering team
- Work requires ability to travel to company locations/meetings including maintaining credit card to pay expenses (to be reimbursed) and driving rental vehicles/flying
- Work may require occasional lifting, carrying, bending
- Ensure Safety program drives goal of zero injuries
- Develop and implement Manufacturing Engineering business plan focused on continuous improvement, productivity, maximizing CAPEX, TPM, and innovation
- Identify resource needs and execute staffing plan
- Utilize strategic thinking and leadership development tools
- Work cross functionally to understand business needs
- Ensure use of performance management, development plans and continuous feedback to develop team
- Achieve exceptional leadership team and solid bench strength.
- Drive regular use of GEMBA, Stage Gate and Kaizens, "walk the talk" by participating in kaizens and pushing use of SBS tools
- Develop into strategic business partner for VP Operations
- Utilize consistent communication and transparency to gain the trust of employees and motivate Manufacturing team to achieve long term growth and financial success
- Achieve success from the company and customer's perspectives
- Track record of delivering results in Manufacturing Engineering capacity
- Success utilizing strategic planning tools including metrics and countermeasures
- Demonstrated application of lean principles to achieve operations excellence
- Ability to use Manufacturing Engineering strategies, including 3D design, drawings, proof-of-concept, design for Manufacturability, material selection, component sourcing, feasibility analysis and product costing to achieve advancements in process and capability
- Successful leadership development with specific examples of mentoring and coaching direct reports
- Excellent communication and presentation skills, and strong level of self-awareness
- Demonstrated ability to execute plan to goals
- Experience creating or maintaining a strong culture promoting safety, respect, and integrity
- Experience increasing employee engagement with specific examples of tools utilized.
- Excellent PC skills including experience with MS Office Suite
- Bachelor's degree in relevant discipline preferred
- 8 to 12 years progressive and related business experience (Manufacturing Engineering preferred)
- Experience with brazing and related factors , including metallurgy, preferred
- Experience with tool and die design, technology and software preferred
- Ability to attend GEMBA and travel throughout production environment to oversee program implementation
- Work requires problem solving skills and ability to analyze data and make rational decisions
- Must be able to communicate with others in a manner that results in clear direction and interaction
- Work requires ability to utilize company computer equipment and software programs
- Work requires ability to understand engineering software programs utilizied by Manufacturing Engineers
- Work requires ability to understand Engineering principles to coach and mentor Engineering team
- Work requires ability to travel to company locations/meetings including maintaining credit card to pay expenses (to be reimbursed) and driving rental vehicles/flying
- Work may require occasional lifting, carrying, bending
- Ensure Safety program drives goal of zero injuries
- Develop and implement Manufacturing Engineering business plan focused on continuous improvement, productivity, maximizing CAPEX, TPM, and innovation
- Identify resource needs and execute staffing plan
- Utilize strategic thinking and leadership development tools
- Work cross functionally to understand business needs
- Ensure use of performance management, development plans and continuous feedback to develop team
- Achieve exceptional leadership team and solid bench strength.
- Drive regular use of GEMBA, Stage Gate and Kaizens, "walk the talk" by participating in kaizens and pushing use of SBS tools
- Develop into strategic business partner for VP Operations
- Utilize consistent communication and transparency to gain the trust of employees and motivate Manufacturing team to achieve long term growth and financial success
- Achieve success from the company and customer's perspectives
- Track record of delivering results in Manufacturing Engineering capacity
- Success utilizing strategic planning tools including metrics and countermeasures
- Demonstrated application of lean principles to achieve operations excellence
- Ability to use Manufacturing Engineering strategies, including 3D design, drawings, proof-of-concept, design for Manufacturability, material selection, component sourcing, feasibility analysis and product costing to achieve advancements in process and capability
- Successful leadership development with specific examples of mentoring and coaching direct reports
- Excellent communication and presentation skills, and strong level of self-awareness
- Demonstrated ability to execute plan to goals
- Experience creating or maintaining a strong culture promoting safety, respect, and integrity
- Experience increasing employee engagement with specific examples of tools utilized.
- Excellent PC skills including experience with MS Office Suite
- Bachelor's degree in relevant discipline preferred
- 8 to 12 years progressive and related business experience (Manufacturing Engineering preferred)
- Experience with brazing and related factors , including metallurgy, preferred
- Experience with tool and die design, technology and software preferred
- Ability to attend GEMBA and travel throughout production environment to oversee program implementation
- Work requires problem solving skills and ability to analyze data and make rational decisions
- Must be able to communicate with others in a manner that results in clear direction and interaction
- Work requires ability to utilize company computer equipment and software programs
- Work requires ability to understand engineering software programs utilizied by Manufacturing Engineers
- Work requires ability to understand Engineering principles to coach and mentor Engineering team
- Work requires ability to travel to company locations/meetings including maintaining credit card to pay expenses (to be reimbursed) and driving rental vehicles/flying
- Work may require occasional lifting, carrying, bending
-
Project Manager Mechanical Engineering
1 week ago
NovaWorks Solutions Manawa, United StatesConnecting people and technologies, creating the perfect match for our clients, and always finding the right experts for each challenge - that is our goal at FERCHAU and that's why we are looking for you: as an ambitious colleague who, like us, wants to take technologies to the n ...
-
Transportation Engineer/Project Manager
4 days ago
Harrison Consulting Solutions Milwaukee, United StatesLeading U.S. engineering consulting firm is seeking a Transportation Engineer/Project Manager for their Milwaukee office · Responsibilities: · Project engineering and management · Set priorities, develop objects, financial management of projects, and hands-on involvement in desig ...
-
Mechanical Engineer/Project Manager
4 days ago
Harrison Consulting Solutions Milwaukee, United StatesTOP ENR Ranked firm looking to add a talented Mechanical Engineer/Project Manager to their Milwaukee team · Responsibilities: · Manage projects · Perform calculations, equipment selections and designs for educational, aviation/port, municipal and industrial buildings · Assist wit ...
-
Manufacturing Engineering Manager
1 week ago
Lucas Milhaupt, Inc Cudahy, United StatesJob DescriptionLucas Milhaupt, Inc. ("Lucas" and/or "the Company") is the most diversified, vertically integrated brazing alloy producer in the United States. We melt, process and fabricate alloys, which allows us to offer our customers high quality product with shorter lead time ...
-
Manufacturing Engineering Manager
1 week ago
Steel Partners LLC Cudahy, United StatesJob DescriptionJob SpecificationLucas Milhaupt, Inc. ("Lucas" and/or "the Company") is the most diversified, vertically integrated brazing alloy producer in the United States. We melt, process and fabricate alloys, which allows us to offer our customers high quality product with ...
-
Manufacturing Engineering Manager
1 week ago
Lucas-Milhaupt Cudahy, United StatesJob DescriptionLucas Milhaupt, Inc. ("Lucas" and/or "the Company") is the most diversified, vertically integrated brazing alloy producer in the United States. We melt, process and fabricate alloys, which allows us to offer our customers high quality product with shorter lead time ...
-
Manufacturing Engineering Manager
3 days ago
Lucas-Milhaupt Cudahy, United StatesJob Description · Lucas Milhaupt, Inc. ("Lucas" and/or "the Company") is the most diversified, vertically integrated brazing alloy producer in the United States. We melt, process and fabricate alloys, which allows us to offer our customers high quality product with shorter lead ...
-
Manufacturing Engineering Manager
3 days ago
Steel Partners LLC Cudahy, United StatesJob Description · Job Specification · Lucas Milhaupt, Inc. ("Lucas" and/or "the Company") is the most diversified, vertically integrated brazing alloy producer in the United States. We melt, process and fabricate alloys, which allows us to offer our customers high quality produc ...
-
Electrical Engineering Engineer
1 week ago
Omega Ventures Cudahy, United StatesThe Delta Group, founded in 1971, is a strong partner for many successful companies in areas such as the automotive industry, industrial automation, building automation, data centers, and renewable energy. With approximately employees, Delta has sales offices, production faciliti ...
-
Manager, Cloud Platform Engineering
2 days ago
SC Johnson Racine, United StatesSC JOHNSON IS A FIFTH-GENERATION FAMILY COMPANY BUILT ON THE SPIRIT OF OUR PEOPLE. We have been leading with purpose for over 130 years, building iconic brands that win the hearts and minds of consumers - such as Raid, Glade, Ziploc and more, in virtually every country around the ...
-
Engineer / Technician as Supplement Manager
1 week ago
Stellar Innovations Brookfield, United StatesBrookfield is not only one of the most important mobility service providers, but also one of the largest engineering firms in Germany. Currently, we have more than engineers working for us, for example in the modernization, maintenance, and procurement of rail vehicles and their ...
-
Engineering Manager
1 week ago
WEC Energy Group Milwaukee, United StatesWEC Energy Group is one of the nation's largest electric generation, distribution and natural gas delivery holding companies. We employ over 7,000 people in our energy companies and service subsidiaries. As a Fortune 500 company, we value and develop our employees who are making ...
-
FusionWorks South Milwaukee, United StatesAbout the Company · Our company is a global leader in automotive interior design. We shape the present and future of the "car" experience. Our headquarters are located in Shanghai and we employ over employees at approximately 110 development and production sites in 18 countries. ...
-
Engineering Manager
1 week ago
Business Control Systems Milwaukee, United StatesJob DescriptionJob Description · We are actively seeking a · Director of Engineering · to spearhead Engineering · initiatives(Electrical/Transformers) · at our client in Roanoke, VA. Prior experience within Electrical, Power, Transformers, Switchgears, etc. would be needed. ...
-
Engineering Manager
2 weeks ago
Clearwing Productions Milwaukee, United StatesJob Details · Job Location · Clearwing Productions Inc - Milwaukee, WI · Position Type · Full Time · Job Category · Management · Description · Function: · This is a key leadership position in the live event production division of Clearwing. The Engineering Manager will lead ...
-
Nexus Innovations Milo, United StatesLocation: 51063 Cologne | Contract type: Full-time/part-time, permanent | Job ID: 797432 · REWE digital - Your Home of IT · We are the home for all techies - or anyone who feels comfortable in the tech world. This is where you belong if you are an IT specialist or future thinker. ...
-
Engineering Manager
1 week ago
We Energies (WE) Milwaukee, United StatesWe Energies, a subsidiary of WEC Energy Group, is seeking an Engineering Manager for our Gas Transmission and Distribution Integrity Team at our Milwaukee, Chicago, or Green Bay locations. This position offers flexibility for a hybrid work arrangement (remote/on-site) with time s ...
-
Field Service Support Manager
2 days ago
Astronautics Corporation of America Oak Creek, United States**What You Will Do**: · This hybrid on-site position is located at our Headquarters in Oak Creek, WI. You will report directly into the Director - Quality Assurance. · **How You Will Do It**: · - Lead a team that contains both on site and remote employees. · - Lead an internation ...
-
Engineering Manager
2 weeks ago
Medtronic Milwaukee, United States**Careers that Change Lives** · Impact patient outcomes. Come for a job, stay for a career. Supporting the Spine operating unit, Medtronic's Milwaukee facility manufactures innovative medical devices that help patients with cervical and lumbar spine instability caused by aging or ...
-
Sales Operations Specialist
2 days ago
Astronautics Corporation of America Oak Creek, United States**What You Will Do**: · We are seeking a Sales Operations Specialist. This is an excellent opportunity for an energetic, highly motivated, organized, self-starter who takes a proactive approach to serving Customers. You will provide effective and responsive support for Astronauti ...
Manufacturing Engineering Manager - Cudahy, United States - Lucas Milhaupt, Inc
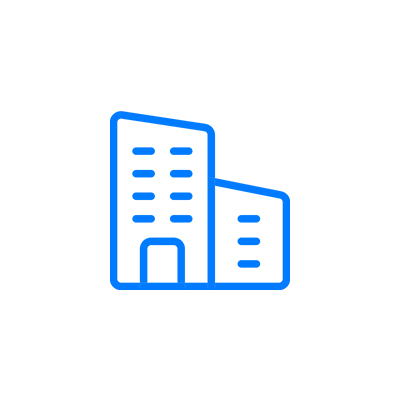
1 week ago

Description
Job DescriptionLucas Milhaupt, Inc. ("Lucas" and/or "the Company") is the most diversified, vertically integrated brazing alloy producer in the United States.
We melt, process and fabricate alloys, which allows us to offer our customers high quality product with shorter lead times and reduced risk to supply disruptions.
With manufacturing facilities in North America, China and France, Lucas Milhaupt is an equal opportunity employer valuing integrity, teamwork, diversity, continuous improvement, urgency and analytical thinking.
Steel Partners Diversified Industrial GroupLucas is part of the Steel Partners Holdings L.P. ("Steel Partners") Diversified Industrial Group.
Steel Partners is a diversified global holding company that engages in multiple businesses through consolidated subsidiaries, associated companies and other interests.
It owns and operates businesses and has significant interests in leading companies in various industries, including diversified industrial products, energy, defense, supply chain management and logistics, banking and youth sports.
Steel Business SystemLucas utilizes the Steel Partners Business System (SBS) to maximize its productivity and eliminate waste.
Using Lean Manufacturing, Design for Six Sigma, Six Sigma, Strategy Deployment and other operational efficiency initiatives that form the foundation of this program, Lucas is committed to embedding continuous improvement within our organization as a means of achieving profitable growth.
Job Title Manufacturing Engineering ManagerLocation Base Cudahy, Wisconsin (Milwaukee)
Reports to VP Operations
FLSA/Compensation Full Time/Salaried/Weekly
Role Summary Lucas is focused on maximizing the efficiency, effectiveness, cost, quality and speed of its manufacturing processes.
The Manufacturing Engineering Manager (MEM) will lead a team to develop and implement manufacturing technologies, process and equipment strategies that achieve this goal.
This key resource will provide leadership for the Manufacturing Engineering group, foster a high level of innovation to fully leverage existing expertise and capital equipment and to develop new, state-of-the-art manufacturing technologies across multiple facilities.
The MEM will actively utilize continuous improvement philosophies and techniques (e.g. lean enterprise, six sigma).The position requires a person who is self-motivated, not afraid to role up their sleeves, natural at trouble-shooting collaboratively and capable of prioritizing work and multi-tasking.
Leadership:
Support Company Culture Promote Safety as number one priority of all employees Ensure business is conducted with integrity, honesty and ethical resolve Foster climate of respect, trust, teamwork and collaboration Support company vision and mission, model values and lead by example Champion environment that demands hard work, celebrates achievement Oversee Manufacturing Engineering Understand "bottom line" concerns that impact Manufacturing goals Translate vision/objectives from strategic thinking into action plans Actively pursue short-term projects while working with the VP of Operations to develop and implement long term Manufacturing Engineering best practices and goals Deliver Targeted Business Results Aggressively manage teams to meet or exceed business goals Implement strong programs that ensure program needs are met Drive use of SBS tools to increase productivity and reduce waste Work cross functionally to maximize efficiency of production teams Maximize use of processes that are repeatable and sustainable Promote Leadership Development Align company goals with the individual goals of those on the team Foster learning environment that encourages employee development Pursue individual growth/development using development plans/coaching Develop succession plans for key positions within Manufacturing Engineering Communicate Powerfully Share company goals/performance to inspire employee action Create high levels of engagement and commitment Convey passion about company and gratitude for employee effort Develop/maintain relationships with key internal and external customers and relevant industry organizations
Key Goals
Demands
Requirements
Lucas Milhaupt, Inc. ("Lucas" and/or "the Company") is the most diversified, vertically integrated brazing alloy producer in the United States.
We melt, process and fabricate alloys, which allows us to offer our customers high quality product with shorter lead times and reduced risk to supply disruptions.
With manufacturing facilities in North America, China and France, Lucas Milhaupt is an equal opportunity employer valuing integrity, teamwork, diversity, continuous improvement, urgency and analytical thinking.
Steel Partners Diversified Industrial GroupLucas is part of the Steel Partners Holdings L.P. ("Steel Partners") Diversified Industrial Group.
Steel Partners is a diversified global holding company that engages in multiple businesses through consolidated subsidiaries, associated companies and other interests.
It owns and operates businesses and has significant interests in leading companies in various industries, including diversified industrial products, energy, defense, supply chain management and logistics, banking and youth sports.
Steel Business SystemLucas utilizes the Steel Partners Business System (SBS) to maximize its productivity and eliminate waste.
Using Lean Manufacturing, Design for Six Sigma, Six Sigma, Strategy Deployment and other operational efficiency initiatives that form the foundation of this program, Lucas is committed to embedding continuous improvement within our organization as a means of achieving profitable growth.
Job Title Manufacturing Engineering ManagerLocation Base Cudahy, Wisconsin (Milwaukee)
Reports to VP Operations
FLSA/Compensation Full Time/Salaried/Weekly
Role Summary Lucas is focused on maximizing the efficiency, effectiveness, cost, quality and speed of its manufacturing processes.
The Manufacturing Engineering Manager (MEM) will lead a team to develop and implement manufacturing technologies, process and equipment strategies that achieve this goal.
This key resource will provide leadership for the Manufacturing Engineering group, foster a high level of innovation to fully leverage existing expertise and capital equipment and to develop new, state-of-the-art manufacturing technologies across multiple facilities.
The MEM will actively utilize continuous improvement philosophies and techniques (e.g. lean enterprise, six sigma).The position requires a person who is self-motivated, not afraid to role up their sleeves, natural at trouble-shooting collaboratively and capable of prioritizing work and multi-tasking.
Leadership:
Support Company Culture Promote Safety as number one priority of all employees Ensure business is conducted with integrity, honesty and ethical resolve Foster climate of respect, trust, teamwork and collaboration Support company vision and mission, model values and lead by example Champion environment that demands hard work, celebrates achievement Oversee Manufacturing Engineering Understand "bottom line" concerns that impact Manufacturing goals Translate vision/objectives from strategic thinking into action plans Actively pursue short-term projects while working with the VP of Operations to develop and implement long term Manufacturing Engineering best practices and goals Deliver Targeted Business Results Aggressively manage teams to meet or exceed business goals Implement strong programs that ensure program needs are met Drive use of SBS tools to increase productivity and reduce waste Work cross functionally to maximize efficiency of production teams Maximize use of processes that are repeatable and sustainable Promote Leadership Development Align company goals with the individual goals of those on the team Foster learning environment that encourages employee development Pursue individual growth/development using development plans/coaching Develop succession plans for key positions within Manufacturing Engineering Communicate Powerfully Share company goals/performance to inspire employee action Create high levels of engagement and commitment Convey passion about company and gratitude for employee effort Develop/maintain relationships with key internal and external customers and relevant industry organizations
Key Goals
Demands
Position Also Available In
Lucas Milhaupt, Inc. ("Lucas" and/or "the Company") is the most diversified, vertically integrated brazing alloy producer in the United States.
We melt, process and fabricate alloys, which allows us to offer our customers high quality product with shorter lead times and reduced risk to supply disruptions.
With manufacturing facilities in North America, China and France, Lucas Milhaupt is an equal opportunity employer valuing integrity, teamwork, diversity, continuous improvement, urgency and analytical thinking.
Steel Partners Diversified Industrial GroupLucas is part of the Steel Partners Holdings L.P. ("Steel Partners") Diversified Industrial Group.
Steel Partners is a diversified global holding company that engages in multiple businesses through consolidated subsidiaries, associated companies and other interests.
It owns and operates businesses and has significant interests in leading companies in various industries, including diversified industrial products, energy, defense, supply chain management and logistics, banking and youth sports.
Steel Business SystemLucas utilizes the Steel Partners Business System (SBS) to maximize its productivity and eliminate waste.
Using Lean Manufacturing, Design for Six Sigma, Six Sigma, Strategy Deployment and other operational efficiency initiatives that form the foundation of this program, Lucas is committed to embedding continuous improvement within our organization as a means of achieving profitable growth.
Job Title Manufacturing Engineering ManagerLocation Base Cudahy, Wisconsin (Milwaukee)
Reports to VP Operations
FLSA/Compensation Full Time/Salaried/Weekly
Role Summary Lucas is focused on maximizing the efficiency, effectiveness, cost, quality and speed of its manufacturing processes.
The Manufacturing Engineering Manager (MEM) will lead a team to develop and implement manufacturing technologies, process and equipment strategies that achieve this goal.
This key resource will provide leadership for the Manufacturing Engineering group, foster a high level of innovation to fully leverage existing expertise and capital equipment and to develop new, state-of-the-art manufacturing technologies across multiple facilities.
The MEM will actively utilize continuous improvement philosophies and techniques (e.g. lean enterprise, six sigma).The position requires a person who is self-motivated, not afraid to role up their sleeves, natural at trouble-shooting collaboratively and capable of prioritizing work and multi-tasking.
Leadership:
Support Company Culture Promote Safety as number one priority of all employees Ensure business is conducted with integrity, honesty and ethical resolve Foster climate of respect, trust, teamwork and collaboration Support company vision and mission, model values and lead by example Champion environment that demands hard work, celebrates achievement Oversee Manufacturing Engineering Understand "bottom line" concerns that impact Manufacturing goals Translate vision/objectives from strategic thinking into action plans Actively pursue short-term projects while working with the VP of Operations to develop and implement long term Manufacturing Engineering best practices and goals Deliver Targeted Business Results Aggressively manage teams to meet or exceed business goals Implement strong programs that ensure program needs are met Drive use of SBS tools to increase productivity and reduce waste Work cross functionally to maximize efficiency of production teams Maximize use of processes that are repeatable and sustainable Promote Leadership Development Align company goals with the individual goals of those on the team Foster learning environment that encourages employee development Pursue individual growth/development using development plans/coaching Develop succession plans for key positions within Manufacturing Engineering Communicate Powerfully Share company goals/performance to inspire employee action Create high levels of engagement and commitment Convey passion about company and gratitude for employee effort Develop/maintain relationships with key internal and external customers and relevant industry organizations
Key Goals
Demands
Salary Range
TBD