- Improve equipment uptime to achieve planned production time of greater than 95%
- Complete all new product development projects on time and on budget
- Achieve or improve OSHA recordable rate as defined by the company and industry
- Maximize effectiveness and completion rate on PM system
- Identify, evaluate and complete facilities work on time and on budget to support business needs
- Reviews and develops designs and layouts for all facilities and production areas
- Estimates labor and material requirements for engineering construction/Facilities projects
- Monitors and insures adherence to regulatory and company safety, environmental and health requirement
- Regular contact with others outside the work group including Contractors, vendors, outside agencies, utility companies and government officials.
- Responsible for project management and timelines
- Keeps abreast of current product developments and trends in areas of expertise
- Performs audits to support facility planning.
- Develops long range plans, conceptual designs, and capital outlay requirements and documentation for facility.
- Formulates and coordinates program specifications, requirements for proposals and contracts, and associated documentsDirectly supervises multiple employees in Maintenance, Facilities, House Keeping and Industrial Engineering. Carries out supervisory responsibilities in accordance with the organization's policies and applicable laws. Responsibilities include interviewing, hiring, and training employees; planning, assigning, and directing work; appraising performance; rewarding and disciplining employees; addressing complaints and resolving problems.
- Bachelor's degree in engineering is preferred.
- 7-10 years of experience managing facilities preferably in a manufacturing environmentTECHNICAL SKILLS
- Electrical, mechanical, hydraulic and pneumatic maintenance and repair.
- Construction, utility and lean manufacturing principles
- Must be able to work at heights.
- Demonstrated ability to read and interpret equipment manuals, work orders, hydraulicschematics, electrical schematics, and pneumatic and mechanical schematics toperform required maintenance and service
- Must have a thorough knowledge of all plant equipment and machinery and the abilityto use precision shop measuring devices and meters
- MS Office Suite
- ERP softwareOTHER SKILLS
- Strong oral and written communication skills and the ability to manage multiplepriorities
- Must be familiar with all industry safety protocols and procedures, including standardenvironmental hazards, health, and conservation guidelinesWhile performing the duties of this Job, the employee is regularly required to stand; walk; sit; use hands to touch, handle, or feel; reach with hands and arms; climb or balance; stoop, kneel, crouch, or crawl; and talk and hear. The employee must regularly lift, push, pull, carry and/or move up to 50 pounds. While performing this Job, the employee is regularly required to exhibit strong manual and spatial dexterity. Specific vision abilities required by this job include close vision, distance vision, color vision, peripheral vision, depth perception and ability to adjust focus.
-
Facilities Engineer
2 weeks ago
Scentbird Somerset, United StatesFacilities Engineer · The facilities engineer will be responsible for the maintenance and improvement of our manufacturing plant. You will be responsible for assessing the facility's resource requirements, designing and optimizing the facility's layout and critical operational s ...
-
Associate Facility Engineer
1 day ago
JCSI Somerset, United StatesJob Description · Job DescriptionASSOCIATE FACILITY ENGINEER · Overview · Join Lupin Pharmaceuticals as we spearhead groundbreaking projects in the pharmaceutical realm, driven by our commitment to innovation. Be at the vanguard, shaping health solutions that matter globally. · ...
-
Facilities Engineer
1 week ago
Actalent Piscataway, United States: · •Lead diagnosing and troubleshooting of complex mechanical/electrical problems and determine corrective measures by referring to blueprints, schematics, repair manuals, parts catalogs, etc. as necessary. · •Recommends production/process equipment or fixtures for purchase ba ...
-
Facilities Engineer
6 days ago
Actalent Piscataway, United StatesThey are the world leader in sustainable natural raw materials. Fragrances, flavors, health and beauty products.Job Title: Facilities EngineerDescription:Main Responsibility: Project management within the plant · •Lead diagnosing and troubleshooting of complex mechanical/electric ...
-
Facilities Engineer
1 week ago
Actalent Piscataway, United States: · •Lead diagnosing and troubleshooting of complex mechanical/electrical problems and determine corrective measures by referring to blueprints, schematics, repair manuals, parts catalogs, etc. as necessary. · •Recommends production/process equipment or fixtures for purchase base ...
-
Facilities Engineer
2 weeks ago
Actalent Piscataway, United StatesThey are the world leader in sustainable natural raw materials. Fragrances, flavors, health and beauty products. · Job Title: Facilities Engineer · Description: · Lead diagnosing and troubleshooting of complex mechanical/electrical problems and determine corrective measures by ...
-
Associate Facility Engineer II Somerset
2 weeks ago
JCSI Somerset, United StatesASSOCIATE FACILITY ENGINEER · Overview · Join Lupin Pharmaceuticals as we spearhead groundbreaking projects in the pharmaceutical realm, driven by our commitment to innovation. Be at the vanguard, shaping health solutions that matter globally. · What You'll Be Doing · Lead t ...
-
Facilities Engineer
2 weeks ago
Ferring Pharmaceuticals Inc. Parsippany, United StatesJob Description: · As a privately-owned, biopharmaceutical company, Ferring pioneers and delivers life-changing therapies that help people build families and live better lives. Our independence helps us cultivate an entrepreneurial spirit and long-term perspective that enables u ...
-
Facility Engineer
4 days ago
Lifetime New York, United StatesPosition SummaryThe Facility Engineer is responsible for: keeping our clubs well maintained and safe; making certain all mechanical systems are working properly including HVAC, plumbing, boilers and more; and to provide a positive experience for our members and guests. No two day ...
-
Facilities Engineer
1 week ago
Powerhouse Arts New York, United StatesJob Description · Job DescriptionPowerhouse Arts is a not-for-profit organization committed to creative expression. Housed in a purpose-built-facility in Brooklyn, the organization hosts an extended network of art and fabrication professionals and educators who work together to c ...
-
Senior Facilities Maintenance Engineer
5 days ago
Insight Global Parlin, United StatesRequired Skills & Experience · 10+ years of experience with Facilities Maintenance Electrical Engineering in medium to large industrial manufacturing and production environments · Extensive experience troubleshooting a wide range of mechanical and electrical equipment and perfor ...
-
Facilities Engineer
1 day ago
PrideStaff Brooklyn, United StatesJob Title:Facilities EngineerShift:The schedule for this position is an 8-hour shift from Monday to Sunday with schedulesbetween 7:30-10:30 pm. Evening and weekend work required.Salary:$80,000 - $90,000Company Information: PrideStaff is seeking a talented Facilities Engineer to j ...
-
Facilities Engineer
4 days ago
Powerhouse Arts New York, United StatesPowerhouse Arts is a not-for-profit organization committed to creative expression. Housed in a purpose-built-facility in Brooklyn, the organization hosts an extended network of art and fabrication professionals and educators who work together to co-create and share artistic pract ...
-
Facilities Engineer
2 days ago
PrideStaff Brooklyn, United States Temporary to HireJob Title:Facilities Engineer · Shift:The schedule for this position is an 8-hour shift from Monday to Sunday with schedules · between 7:30-10:30 pm. Evening and weekend work required. · Salary:$80,000 - $90,000 · Company Information: PrideStaff is seeking a talented Facilities E ...
-
Facilities Engineer
1 week ago
TEKsystems New York, United StatesJob Description · Job DescriptionTEKsystems is seeking a Operations & Maintenance Supervisor to join a large multi-national technology company in New York, NY. · 1. The ability to read engineering design drawings. This could be electrical, controls or mechanical. · 2. Understand ...
-
Facilities Engineer
2 weeks ago
Powerhouse Arts New York, United StatesPowerhouse Arts is a not-for-profit organization committed to creative expression. Housed in a purpose-built-facility in Brooklyn, the organization hosts an extended network of art and fabrication professionals and educators who work together to co-create and share artistic pract ...
-
Facilities Electrical Engineer
6 days ago
Hays Recruitment Newark, United StatesHays InvestorWork for HaysAbout UsFind UsUS EN For Job SeekersFor OrganizationsAustraliaAustriaBelgiumBrazilCanadaChileChinaColombiaCzech RepublicDenmarkFranceGermanyHong Kong SARHungaryItalyJapanLuxembourgMalaysiaMexicoNetherlandsNew ZealandPolandPortugalRomaniaSingaporeSpainSwe ...
-
Critical Facility Engineer
2 weeks ago
BGIS New York, United StatesJob Description · Job DescriptionBGIS is currently seeking a Critical Facility Engineer (Data Center) to join the team in New York, NY. · BGIS is a leading provider of integrated real estate management services, including facilities management, project management, energy & sustai ...
-
Critical Facility Engineer
3 weeks ago
BGIS Secaucus, United StatesJob Description · BGIS is currently seeking a · Critical Facility Engineer · to join the team in · Secaucus, NJ . · BGIS is a leading provider of integrated real estate management services, including facilities management, project management, energy & sustainability services ...
-
Facilities Electrical Engineer
5 days ago
Hays Recruitment Newark, United StatesHays Investor · Work for Hays · About Us · Find Us · US EN · For Job Seekers · For Organizations · Australia · Austria · Belgium · Brazil · Canada · Chile · China · Colombia · Czech Republic · Denmark · France · Germany · Hong Kong SAR · Hungary · Italy · Ja ...
Facilities Engineer - Somerset, United States - Micro Manufacturing Solutions for Life
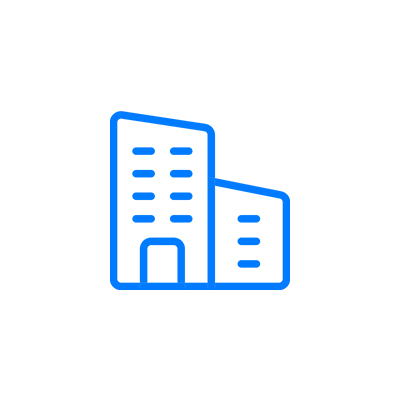
1 month ago

Description
The Facilities Engineer is responsible to coordinate and direct the design, planning, construction, maintenance, and alteration of equipment, machinery, buildings and associated utilities.
The Facilities Engineer is expected to:
EDUCATION AND EXPERIENCE
While performing the duties of this Job, the employee is regularly exposed to moving mechanical parts; risk of electrical shock and vibration.
The employee is frequently exposed to high precarious places, wet and/or humid conditions and odors, dusts, mists, fumes or airborne particles and toxic or caustic chemicals.
The employee is occasionally exposed to high, precarious places and outside weather conditions. The noise level in the work environment is usually loud.