Planner & Production Scheduler - Glen Burnie, United States - ADDMAN Precision - Baltimore
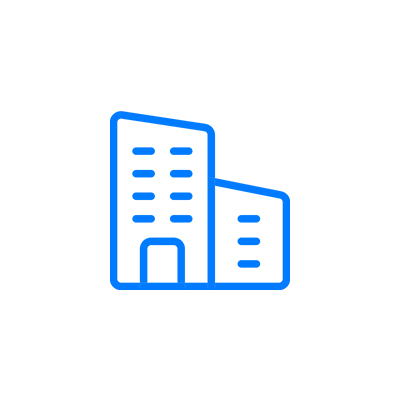
3 weeks ago
Description
:***:
ESSENTIAL JOB FUNCTIONS:
- Master Production Scheduling
Collaborate with cross-functional teams, including production, sales, and logistics, to develop and maintain a comprehensive master production schedule. Ensure production plans are aligned with sales forecasts, inventory levels, and capacity constraints.
- Inventory Management
Regularly monitor and analyze inventory levels to prevent stockouts and overstock situations. Implement inventory control strategies to optimize inventory turnover while minimizing carrying costs.
- Purchase Order Management
Create, issue, and manage purchase orders for materials and services in accordance with production schedules and inventory targets. Coordinate with suppliers to ensure on-time delivery of goods and services.
- Supplier Relationship Management
Build and maintain strong relationships with suppliers to facilitate efficient procurement processes, negotiate favorable terms, and resolve any supply-related issues promptly.
- Cost Optimization
Work closely with the finance team and vendors to negotiate competitive pricing and terms. Identify opportunities to reduce procurement costs while maintaining the highest quality standards.
- Demand Forecasting
Utilize historical data, market trends, and input from sales and marketing teams to develop accurate demand forecasts. Adjust production plans and inventory levels based on demand fluctuations.
- Risk Management
Identify potential supply chain risks, such as shortages or disruptions, and develop contingency plans to mitigate their impact on production and operations.
- Continuous Improvement
Actively participate in process improvement initiatives to enhance supply chain efficiency, reduce lead times, and optimize overall performance.
- Data Analysis and Reporting
Utilize various tools and systems to gather and analyze data related to supply chain performance, vendor performance, and inventory levels.
Prepare regular reports for management review.- Compliance
Ensure all procurement activities comply with company policies, industry regulations, and ethical standards.
- Perform other duties as assigned
- Punctual attendance
- Follow all Company policies and procedures
Requirements:
QUALIFICATIONS:
- 35 years of working in an office environment
- Master Production Scheduling
Collaborate with cross-functional teams, including production, sales, and logistics, to develop and maintain a comprehensive master production schedule. Ensure production plans are aligned with sales forecasts, inventory levels, and capacity constraints.
- Inventory Management
Regularly monitor and analyze inventory levels to prevent stockouts and overstock situations. Implement inventory control strategies to optimize inventory turnover while minimizing carrying costs.
- Purchase Order Management
Create, issue, and manage purchase orders for materials and services in accordance with production schedules and inventory targets. Coordinate with suppliers to ensure on-time delivery of goods and services.
- Supplier Relationship Management
Build and maintain strong relationships with suppliers to facilitate efficient procurement processes, negotiate favorable terms, and resolve any supply-related issues promptly.
- Cost Optimization
Work closely with the finance team and vendors to negotiate competitive pricing and terms. Identify opportunities to reduce procurement costs while maintaining the highest quality standards.
- Demand Forecasting
Utilize historical data, market trends, and input from sales and marketing teams to develop accurate demand forecasts. Adjust production plans and inventory levels based on demand fluctuations.
- Risk Management
Identify potential supply chain risks, such as shortages or disruptions, and develop contingency plans to mitigate their impact on production and operations.
- Continuous Improvement
Actively participate in process improvement initiatives to enhance supply chain efficiency, reduce lead times, and optimize overall performance.
- Data Analysis and Reporting
Utilize various tools and systems to gather and analyze data related to supply chain performance, vendor performance, and inventory levels.
Prepare regular reports for management review.- Compliance
Ensure all procurement activities comply with company policies, industry regulations, and ethical standards.