Quality Coordinator - Tucson, United States - Apex Microtechnology
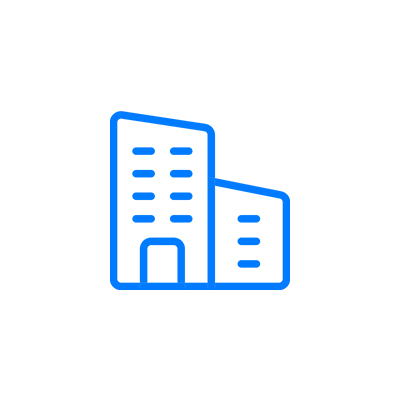
1 week ago
Description
The Quality Coordinator will support the execution of manufacturing goals by leading continuous improvement through problem-solving and quality improvement tools and techniques.
Essential functions and Responsibilities:
Key responsibilities will include but not be limited to:
- Drafts and maintains records and documentation of training and procedures
- Collect RoHS/Reach information at the material and final device level and support customer inquiries requesting RoHS and REACH surveys.
- Review records and complete paperwork/computer entry information
- Drive improvements across multiple departments such as Design, Customer Service, Applications, and Operations
- Review customer drawings to identify potential exceptions to Apex's standard processes and report these to the quality manager
- Perform customer return analysis to determine root cause and corrective/preventative actions.
- Collect data, perform analysis, and flowchart processes in support of driving continual improvement
- Review engineering change notices for accuracy and issue deviation reports
- Knowledge of, or willingness to learn process flowcharting and statistical process control
- Ability to provide feedback and instruction to others in a constructive manner
- Ability to work well with others in a team environment and work towards a common goal. Performs other related duties as requested or required.
- Identify solutions and/or complete assigned tasks related to the resolution of corrective and preventive actions, internal audit findings, and nonconformance reports.
- Ability to maintain quality programs, including tracking, analyzing, reporting, and problem solving.
- Assist in internal and external corrective action plans to reduce product yield loss, and customer failure analysis information.
- Perform adequacy reviews for flow down of QA requirements to implementing documents and quality affecting processes.
- Assist in development of quality system processes, i.e., etc.
- Assist in defining/developing Quality Program performance indicators, measurements, and reporting requirements.
- Work closely with Operations and other departments to ensure an appropriate level of quality tools and techniques.
- Perform internal audits.
- Assist with customer, Registrar, and Government audits.
Minimum Qualifications:
- 2+ years' experience leading Continuous Improvement efforts using process methods and tools, across multiple functions
- Comfortable working with multiple departments.
- Excellent verbal and written communication skills and the ability to relate to diverse teams and functions.
Preferred Qualifications:
- Understanding of a quality system and its development, documentation, and implementation with respect to ISO9001 and MIL-PRF38534 requirements.
- 4+ years' experience in Continuous Improvement efforts using Lean process methods and tools, across multiple functions of the business
- 4+ years participating in Continuous Improvement projects
- Six Sigma Black Belt Certification
- Experience running Design of experiments.
- Experience on the overall product development process/cycle, from early customer engagement to project success meeting all specifications
- Experience with ISO, DLA, Internal and Customer Audits.
More jobs from Apex Microtechnology
-
Manufacturing Maintenance Technician
Tucson, United States - 3 days ago
-
Product Test Engineer
Tucson, United States - 1 week ago