- Maintains an understanding of customer requirements (including AQL Sampling, PPAP, FAIRs, Capability Studies, Quality Documentation, Gage R&R's, etc.) and ensures plans and documentation meet these requirements.
- Coordinates with inspection teams to ensure that plans effectively meet data collection needs and data is captured as effectively as possible.
- Utilizes and develops risk management tools and aids for use by the organization in accordance with documented procedures, including but not limited to PPAP, PFMEA, DFMEA, etc. Develops process mitigation plans and strategies that are designed to mitigate the risks identified through the Risk Management process.
- Communicates with customers and suppliers regarding quality planning processes.
- Ensures process compliance through use of procedures, work instructions, flowcharts, forms, templates, checklists, worksheets, and other product and process related documentation.
- Performs a broad variety of tasks as assigned by manager.
- Lead and Hold Accountable the Quality Planning team.
- Continued development of ZDP process, inspection strategy, and overall efficacy of team
- Ensure plans and are in place for all jobs as necessary (NPI, process/revision changes, time lapses, etc.).
- Ensures effective use of quality plans and programs by inspection and production teams by responding to issues and concerns and providing necessary raining.
- Ability to communicate effectively with all internal and external customers in both written and oral form.
- Knowledge of Quality Planning, zero defect planning, CMM Programming, and quality documentation.
- Understanding of quality and inspection specifications, including but not limited to: AS9102, AS13002, etc.
- Ability to perform statistical process control input and interpret statistical data to compensate for machining deviation.
- Ability to generate and update quality documents and tools, such as control plans, FMEAs, PPAP, FAIRs, etc.
-
Quality and Food Safety Supervisor
2 weeks ago
Post Consumer Brands Meadville, United States Full timeResponsibilities · Responsible for the Quality, Food Safety, Leadership and Focused Improvement results of a team of hourly Laboratory Technicians and Quality Coordinators Works with all site teams to address quality concerns and leads or assists in resolution Role models our Bas ...
-
Automotive Sales Consultant
2 weeks ago
McCandless Ford Meadville Meadville, United StatesWhat We're Looking For: · McCandless Ford Meadville is growing? Are you energetic and ambitious? Do you like to talk with people and enjoy the rush in closing a deal, then we are looking you to join our Sales family. APPLY TODAY · What We Offer · Potential commission earnings $40 ...
-
Archives and Special Collections Librarian
2 weeks ago
InsideHigherEd Meadville, United StatesArchives and Special Collections Librarian June 4th 2024 · Tagged: LibraryROLE TITLE: Archives & Special Collections Librarian · REPORTS TO: Dean of the Library · Summary of Position · Preserves, protects, and promotes Allegheny's history in alignment with the Libraries' mission ...
-
KI Kinetic Ops
1 week ago
Windstream Communications Meadville, United StatesJob Description · Windstream Holdings, Inc., is a leading provider of advanced network communications and technology solutions for consumers, small businesses, enterprise organizations and carrier partners across the U.S. · * As Kinetic, Windstream offers bundled services, incl ...
-
Assistant Director of Operations
2 weeks ago
Parkhurst Dining Meadville, United StatesParkhurst Dining, part of the Eat'n Park Hospitality Group, is a family owned, family run company that provides culinary, dining and catering services to over 80 organizations and universities east of the Mississippi. We believe that food is best when made from scratch with local ...
-
Assistant Director of Operations
2 weeks ago
Eatn Park Hospitality Group Meadville, United States Full timeParkhurst Dining, part of the Eat'n Park Hospitality Group, is a family owned, family run company that provides culinary, dining and catering services to over 80 organizations and universities east of the Mississippi. We believe that food is best when made from scratch with local ...
-
Industrial Controls Engineer
1 week ago
Vitro Meadville, United StatesOverview: · Vitro is the largest glass manufacturer in the Western Hemisphere and the largest glass producer in North America. Vitros glass products can be found in some of the most iconic vehicles on the road, in countless buildings and homes around the world, and in billions o ...
-
KI Kinetic Ops
1 week ago
Windstream Meadville, United StatesWindstream Holdings, Inc., is a leading provider of advanced network communications and technology solutions for consumers, small businesses, enterprise organizations and carrier partners across the U.S. · As Kinetic, Windstream offers bundled services, including premium broadba ...
-
KI Kinetic Ops
1 week ago
Windstream Communications Meadville, United StatesKI Kinetic Ops - Customer Service Technician · Meadville, PA 16335, USAReq #784 · Monday, May 6, 2024 · Windstream Holdings, Inc., is a leading provider of advanced network communications and technology solutions for consumers, small businesses, enterprise organizations and ca ...
-
benefits advisor
1 week ago
the djb group Meadville, United StatesThis is a truly rewarding Business-to-Business position that offers one of the strongest compensation structures in the industry. If youre outgoing, entrepreneurial and motivated, it might be time to unleash your potential as a Voluntary Benefits Specialist. With the djb group ba ...
-
Benefits Advisor
2 weeks ago
the djb group Meadville, United StatesThis is a truly rewarding Business-to-Business position that offers one of the strongest compensation structures in the industry. If youre outgoing, entrepreneurial and motivated, it might be time to unleash your potential as a Voluntary Benefits Specialist. With the djb group ba ...
-
Quality and Food Safety Supervisor
4 weeks ago
Post Consumer Brands Meadville, United StatesBusiness Unit Overview: · Headquartered in Lakeville, Minn., Post Consumer Brands, a business unit of Post Holdings, Inc., is dedicated to providing people and their pets with delicious food choices for every taste and budget. The companys portfolio includes beloved brands such a ...
-
Production Supervisor
3 weeks ago
Manufacturer-Steel Fabrication Meadville, United StatesJob Description · Job DescriptionSummary: Supervises and coordinates activities of production workers to attain production and quality goals, maintains all shop floor control methods and analyzes data to guide improvement with various Team Leaders. Communicates and administers co ...
-
Senior Process Control Engineer
1 week ago
Vitro Meadville, United StatesOverview: · Vitro is the largest glass manufacturer in the Western Hemisphere and the largest glass producer in North America. Vitros glass products can be found in some of the most iconic vehicles on the road, in countless buildings and homes around the world, and in billions o ...
-
Registered Nurse
6 days ago
Corporate Positions Meadville, United StateseKidzCare is hiring a talented Registered Nurse (RN) Supervisor for our office in Meadville, PA. This position includes local travel throughout the Mercer county and surrounding areas.**This is a hybrid position with some in office and remote working capabilities**Benefits Hybrid ...
-
Family Based Counselor
21 hours ago
George Junior Republic Meadville, United StatesJob Description · Job DescriptionAbout George Junior Republic:Founded in 1909, George Junior Republic is dedicated to helping at-risk youth become successful, well-adjusted adults, capable of achieving a higher degree of citizenship and a better understanding of his responsibilit ...
-
Veterinarian
4 weeks ago
Conneaut Lake Veterinary Hospital Meadville, United StatesJob Description · Conneaut Lake Veterinary Hospital of Meadville, Pennsylvania is excited to add another veterinarian to our team We could use the help of a seasoned veterinarian as we continue to grow our practice. · Our doctors' pride themselves on staying up to date with curre ...
-
Project Engineer
1 week ago
Acutec Precision Aerospace Inc. Meadville, United StatesJob Type · Full-time · Description · The Project Engineer is a key manufacturing role responsible for researching, designing , implementing, and testing the manufacture of key parts and assemblies. Requires technical knowledge of machining processes, a strong understanding of t ...
-
Mixing Team Lead
1 week ago
Michael Foods Meadville, United StatesBusiness Unit Overview · Headquartered in Lakeville, Minn., Post Consumer Brands, a business unit of Post Holdings, Inc., is dedicated to providing people and their pets with delicious food choices for every taste and budget. The company's portfolio includes beloved brands such ...
-
Mixing Team Lead
2 weeks ago
Post Holdings Meadville, United StatesBrand: Post Consumer Brands · Categories: Operations Production · Locations: Meadville, Pennsylvania · Position Type: Regular Full-Time · Remote Eligible: No · Req ID: 23554 · Job Description · Business Unit Overview · Headquartered in Lakeville, Minn., Post Consumer Brands, a bu ...
Quality Planning Lead - Meadville, United States - Acutecind
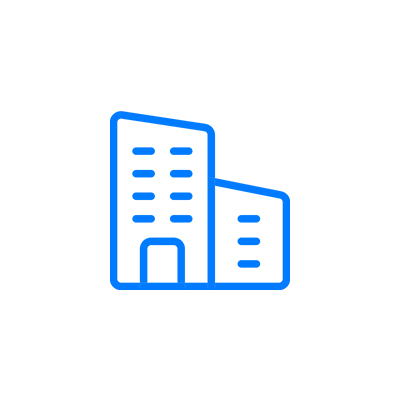
1 month ago

Description
Reporting to the Director of Quality, the Quality Planning Lead is a working lead role that will be responsible for leading the Quality Planning team with a focus on throughput and quality of Zero-Defect Planning (ZDP).
This position will also be responsible for the continued development of the ZDP process, inspection strategy, and other projects that increase the overall efficacy of the Quality team.
Essential Duties and ResponsibilitiesTo perform this job successfully, an individual must be able to perform each essential duty satisfactorily. The requirements listed below are representative of the knowledge, skill, and/or ability required. Reasonable accommodations may be made to enable individuals with disabilities to perform the essential functions.
Education & Experience Requirements:
Bachelor's degree in an Engineering discipline and/or at least five years experience in a related field. Six Sigma Green-Belt or other process improvement experience is a plus.
Required Knowledge and Skills:
This position will directly supervise Quality Documentation Team and Quality Engineering – Planning Team.
May be required to train and assist other employees.
Physical Demands
The physical demands described here are representative of those that must be met by an employee to successfully perform the essential functions of this job.
Reasonable accommodations may be made to enable individuals with disabilities to perform the essential functions.While performing the duties of this job, the employee is regularly required to walk; and regularly required to stand; handle, or feel and reach with hands and arms.
The employee will regularly lift and/or move up to 5 to 10 pounds and rarely lift and/or move up to 50 pounds.
Specific vision abilities required by this job include color vision, depth perception, and the ability to adjust focus. Annual employee vision tests are administered.Work Environment
The work environment characteristics described here are representative of those an employee encounters while performing the essential functions of this job.
Reasonable accommodations may be made to enable individuals with disabilities to perform the essential functions.While performing the duties of this job, the employee is regularly exposed to moving mechanical parts, fumes, or airborne particles.
The noise level in the work environment is frequently loud.Safety and Policy Practices
The employee in this job must be knowledgeable in regard to the safety policies and procedures of the Company as described in the company safety manual.
The employee must adhere to all said policies and procedures while supporting the goals and objectives of the organization and recognize the Company's need to achieve its business objective.
Employee is responsible for complying with Company hazardous waste disposal procedures.#J-18808-Ljbffr