Core Lead Production Supervisor - Kenosha, United States - Engendren Corporation
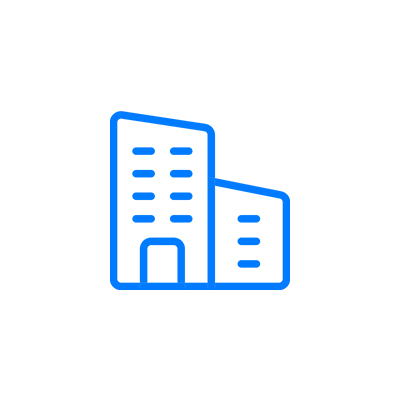
3 weeks ago
Description
COME JOIN OUR TEAM
Job Summary:
The Core Department Supervisor provides area leadership and direct supervision to Core department Lead and production employees.
In addition, the Supervisor will perform all Core Department procedures (e.g., fin and tube prep, soldering, testing, etc.) as necessary.
The Production Supervisor receives specific production goals and limited direction from the Operations Manager, Director of Operations, and the planning department, develops work plans by combining long-term company strategies with specific assignments, and resolves most problems independently.
The Supervisor is directly responsible for the safety, performance, efficiency, utilization, on-time delivery, and quality of all work in the Core Department and is expected to constantly monitor and help control labor and material costs.
Essential Duties and Responsibilities include the following, with other duties assigned as necessary**:
- Directs and oversees all staff and operations on a particular shift—responsible for all employees, processes, equipment, time, and production records.
- Schedules employees and plans workflow according to production capabilities and schedule.
- Supervises core department production employees, assumes administrative duties not limited to attendance point system record keeping, time off request forms, promotion and transfer forms, disciplinary, training rosters, and coaching forms.
- Oversee and ensure execution of daily production schedules.
- Troubleshoot production related problems and monitor and maintain performance of departments to meet or exceed KPI goals.
- Hire, train, coach, motivate, evaluate, and mentor team members.
- Develop and implement training documentation, work instructions, onboarding procedures, and employee development plans.
- Collaborates with Engendren's Human Resources, Engineering, Production, Planning, Purchasing, Materials, and Manufacturing Engineering departments.
- Participate in all production meetings, generate, publish, and present weekly and monthly KPI reports, and review schedule status daily.
- Initiates/reviews job orders (written or verbal) and establishes/interprets manufacturing specifications.
- Upholds safety rules, work rules, company policies, counsels' employees, and initiates disciplinary measures where appropriate.
- Monitors workinprogress and spotchecks completed work to ensure that standards are met.
- Advises company management on technical core manufacturing issues and recommends changes.
- Ensures that preventative maintenance schedules are maintained for core department equipment.
- Identifies and corrects problems and inefficiencies in processes, materials, equipment, or skills.
- Ensures compliance with federal, state, local, and organizational laws, regulations, guidelines, and best practices, including those related to safety and health.
- Trains all employees to maintain staff proficiency for all area tasks.
- Ensures that work areas, equipment, and other tools of the trade are clean and properly maintained.
- Works in a safe manner at all times, ensures that safety rules are followed without exception, and participates in any and all company safety programs and initiatives.
- Ensures that all work is done in accordance with and adherence to IEA's ISO and Quality standards.
- Reasonable accommodations may be made for individuals with disabilities to perform essential duties.
- Thorough understanding of raw materials, production processes, quality control, cost management, and other effective manufacturing and distribution techniques.
- Strong supervisory and leadership skills.
- Strong analytical and problemsolving skills.
- Proficient with Microsoft Office Suite or related software.
- Performs other duties as assigned.
Physical Demands:
- Maximum lifting requirement (pounds): 100 (infrequently), 50 (occasionally), 25 (frequently).
- Maximum moving requirement (pounds): 100.
- Maintaining physical condition necessary for the following: frequent standing, walking, kneeling, crouching, stooping, squatting, and twisting upper body; infrequent climbing or sitting.
- Working at heights off the ground up to: 15 feet.
- Vision requirements: Close, distance, and peripheral vision; depth perception.
Work Environment:
- Work location: Soldering booth, metal fabrication/assembly shop, and shop office with computer.
- Exposure to: Fumes, airborne particles, wet/humid (nonweather) conditions, toxic/caustic chemicals, moving mechanical parts/equipment.
- Personal protective equipment requirement: Respirator (for soldering), safety glasses, safety shoes, and ear protection.
Position Requirements:
- Key skills, abilities, and knowledge:
- Ability to communicate and work with others and lead immediate subordinates.
- Ability to organize and direct work activities in a fastpaced, shop environment.
- Working knowledg
More jobs from Engendren Corporation
-
Fabrication Machine Operator
Kenosha, United States - 2 weeks ago