Machining Supervisor - Endicott, United States - George Industries
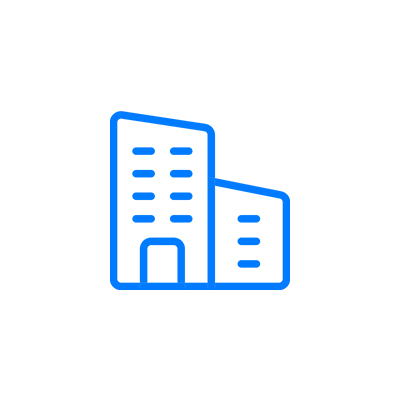
1 week ago
Description
***The machining supervisor oversees all aspects of machining operations. Their primary role is to ensure that machining processes are conducted efficiently, safely, and to high quality standards. They are responsible for leading and supervising a team of machinists and machine operators, coordinating production schedules, monitoring machine performance, and enforcing safety protocols. They work with the machinists to optimize productivity, minimize downtime, and drive continuous improvement initiatives to enhance machining processes and achieve production goals. They collaborate with other departments such as production planning, quality assurance, maintenance, and materials management (PC) to ensure smooth operations and meet customer requirements.DUTIES AND RESPONSIBILITIES
- _Production Planning and Scheduling: _Develop production plans, schedules, and priorities based on customer orders, production capacity, and resource availability. Coordinate with production planners, materials managers, and other departments to ensure timely and efficient machining operations.
- _Team Leadership and Management: _Supervise and lead a team of machinists, machine operators, and support staff. Provide guidance, direction, and support to ensure that team members understand their roles, responsibilities, and performance expectations. Foster a positive work environment, promote teamwork, and address any issues or conflicts that may arise.
- _Quality Assurance and Control_: Ensure that machined parts meet quality standards, specifications, and customer requirements. Implement quality control measures, inspection procedures, and process controls to monitor and maintain product quality throughout the machining process. Investigate and address any quality issues or deviations from standards promptly.
- _
Machining Operations Oversight:
_Oversee machining operations, including CNC machining, milling, turning, grinding, and other machining processes. Monitor machine performance, tool wear, and machining parameters to optimize productivity, minimize downtime, and maximize efficiency.
- _
Safety Compliance:
_Promote and enforce safety protocols, procedures, and regulations to ensure a safe working environment for all employees. Conduct safety inspections, audits, and training sessions to identify hazards, mitigate risks, and prevent accidents or injuries_._
- _Equipment Maintenance and Reliability: _Coordinate equipment maintenance, repairs, and routine preventive maintenance activities to ensure optimal performance and uptime. Work closely with maintenance technicians and engineers to address equipment issues, troubleshoot problems, and minimize downtime.
- _
Inventory Management:
_Monitor inventory levels of raw materials, tooling, and supplies.
Coordinate with materials management and procurement teams to ensure that materials and tooling are available as needed for machining operations, minimize stockouts, and optimize inventory turnover.
- _Performance Monitoring and Reporting: _Track machining metrics, key performance indicators (KPIs), and performance targets. Analyze machining data, identify trends, and report on performance to senior management. Implement corrective actions or improvements as needed to achieve production goals.- _Training and Development: _Provide training, coaching, and development opportunities to machinists and machine operators to enhance their skills, knowledge, and performance. Identify training needs, conduct skills assessments, and develop training plans to support individual and team growth.
- Provide value to our customers by using Lean tools and concepts to identify and eliminate waste in all forms (scrap/rework, transportation, motion, waiting, inventory, over production, over processing, and underutilization of people). Uses systemic thinking by seeing processes from end to end and works to challenge the status quo to eliminate the root cause of problems. Is involved in individual and/or team activities that involve using Lean tools and concepts to improve the flow of information and material.
- Other duties assigned as needed
KEY PERFORMANCE METRICS
- Productivity through department
- First time quality
PHYSICAL REQUIREMENTS
- Must be able to lift 1020 pounds frequently, and up to 50 pounds periodically.
- Must be able sit, stand or walk for up to 8 hours.
MINIMUM REQUIREMENTS
- Education: A high school diploma or equivalent experience. Prefer postsecondary education such as an associate's or bachelor's degree in a relevant field such as engineering, manufacturing, operations management, or business administration.
- Experience: Several years of experience in manufacturing or production, including experience in a supervisory or leadership role.
- Technical Knowledge: Strong understanding of machining processes, procedures, and best practices. Machines include, CNCs, Lathes, Mills, among others.
- Leadership Skills: Demonstrated leadership and management abilities, in
More jobs from George Industries
-
Quality Inspector Lead/document Control
Endicott, United States - 3 weeks ago