- · 5+ years of experience in manufacturing environment
- · Trained in problem solving per CQI-20 (preferred but not required)
Quality Engineer - Lincolnwood, United States - EJOT ATF
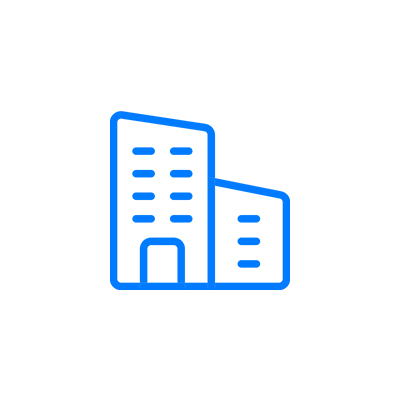
1 month ago

Description
Quality Engineer
Reports To: Director of Quality
Position Description: Resolution of problem when customer receives a non-conforming part.
Customers will see products from EJOT ATF that at times do not meet written or unwritten product requirements. In these instances, customers need a technical resource that can resolve the issue. This role requires containment of the issue, quick resolution (may not be the complete fix due to customer driven time constraints) and understanding of the customer's perspective on severity of the problem. The role requires working with the team where the process is completed including suppliers.
1. Define / Identify:
1.1. Receive customer notifications for problems via any communication means that the customer deems fit.
1.2. Log-in the issue to customer complaints tracking database
1.3. Organize response that includes:
1.3.1. Determining the condition to contain (Stop the condition from reaching the customer)
1.3.2. Completing containment activities: Creating quality alerts, defining sorting criteria and organizing sorting activity, certifying product based on this sort, defining clean point for containment.
1.3.3.Define problem statement to the supplier through SCAR (Supplier Corrective Action Request) initiation (as needed)
1.4. Define problem statement
2. Measure: This role requires the ability to understand the time constraint vs problem solving as #FixItForever and act accordingly.
2.1. Collect data, facts and findings that convert to root cause analysis
2.2. Determine conditions that were unique to the work order / part when the defect was created
2.3. Update PFMEA based on findings
2.4. Track containment costs that will be forwarded to the supplier upon issue resolution (as needed)
3. Analyze: This role requires the ability to understand the time constraint vs problem solving as #FixItForever and act accordingly.
3.1. Data from gainseeker regarding product dimensional history, data from Tooling software to understand tool usage and, data from Final Inspection and Quality Concerns log
3.2. Formalize a team with support from engineering and manufacturing to determine root cause. Escalate as needed.
3.3. Use Fishbone methodology along with Is / Is Not to determine root cause.
3.3.1.In cases where root cause is not singular, analyze data to create variation models to show how multiple root causes influence the final output of defects.
3.4. Devise tests and experiments to validate root cause.
3.5. For root cause in supplier-controlled processes:
3.5.1.Formalize a team with the supplier to determine root cause. Escalate as needed.
3.5.2.Devise tests and experiments to validate supplier root cause. May require supplier on-site visit.
4. Improve:
4.1. Determine corrective action or improvement to the process. Note that most times, this might be an improvement on the containment actions as defined in (1) but look for quick data-driven corrections to the process that can yield improvements. Understand that quick improvements are sometimes better than slow complete fixes.
4.2. Formalize a team with support from engineering and manufacturing to implement corrective action. Escalate as needed.
4.3. Create plan for implementation of the corrective action
4.4. For root cause in supplier-controlled processes:
4.4.1. Formalize a team with the supplier to implement corrective action. Escalate as needed.
4.4.2. Follow-up on corrective action implementation at the supplier.
5. Control:
5.1. Define controls to ensure improved process continues to operate as intended and controls alert when the process is operating outside parameters.
5.2. Formalize a team with support from engineering and manufacturing to ensure implementation of new controls. Escalate as needed.
5.3. Determine clean point for customer with applied corrective action.
5.4. For root cause in supplier-controlled processes:
5.4.1.Guide supplier in defining controls to ensure improved process continues to operate as intended and controls alert when the process is operating outside parameters.
5.4.2.Formalize a team with the supplier to ensure implementation of new controls. Escalate as needed.
5.4.3.Determine clean point from the supplier and to the customer with applied corrective action.
6. Verify Controls:
6.1. Create and manage verification of corrective action
6.2. Define duration of certification sort to validate effectiveness of corrective actions
6.3. Measure updated occurrence and detection.
6.4. Update PFMEA and control plans or transfer information to PPAP team to update documents.
6.5. For root cause in supplier-controlled processes:
6.5.1.Follow-up on verification of corrective action.
6.5.2.Define duration of certification sort to validate effectiveness of corrective actions.
6.5.3.Guide supplier to measure updated occurrence and detection and update PFMEA and control plans.
Knowledge: -
· Cold Forming 101
· Fastener manufacturing processes – baseline knowledge of heading, rolling, heat treatment, plating, thread masking / patching, sort, and packaging
· Baseline function and use case for PFMEAs and Control Plans – how these are living documents that document an organizations lessons learned and improvements
· Material Flow in cold state
· Use case for problem solving tools: Fishbone, 5Why.
· DMAIC (Define, Measure, Analyze, Improve Control) thought process for process improvement
· Statistical analysis tools (Model development, Regression analysis, Cpk review, analysis of means and variances)
· Customer applications / how are EJOT ATF parts applied or used by the customer.
· Internal EJOT ATF systems – CMS procedures and material flow to make decisions and complete the task of assigning disposition (Sort, Scrap or Rework) to suspect parts
Skills: -
· Great communication skills. Be able to describe the problem and status of the work succinctly with data and we able to bring a sense of calm to the communication
· Use of MINITAB – statistical analysis
· Use of problem-solving tools: Fishbone, 5Why
· Measure parts, compile and analyze data
· Demonstrated capabilities with Microsoft Office Suite
· Project and task management for internal and external tasks
· Serving the customer – listen and note details. Be the solver not the empathizer.
Ability: -
· To observe and attain information from multiple sources as facts and findings behind the cause of a product non-conformance
· To assign corrected or adjusted ranking for Occurrence and Detection on current PFMEA
· To understand what data to look for to understand the scope of the problem along with variables that affect the output (creating the problem) – use of Fishbone.
· To extract and attain data from existing systems and tools at EJOT ATF
· To combine data and to understand what variables affect the outcome and to what degree
· To define controls on the process to ensure that the applied corrective action has the expected outcome.
· To speak with data and understand what customer requests are warranted vs not warranted. Not warranted requests must be dealt with carefully through data. Escalate to Director of Quality as needed as these conversations can get tough.
· To understand timing for providing data. Provide data as recorded – Integrity as its core. Provide bad news with the understating of its effect on potential new requests from the customer and how EJOT ATF can be protected along with ensuring that the customer has reduced concerns from the data.
· Disclose the problem along with potential solutions as options.
Traits: -
· Timely response: Great follow-up. No missed deadlines. Provide realistic timelines and ensure that they are achieved without compromise.
· EJOT ATF Core value: Servant leadership. This role's service to the organization and to the customer is to relieve the concern that the customer has for using the non-confirming product. This is via stopping the flow of non-conforming product to the customer (most likely path) OR relieving the customer of the concern and understanding the product as seen is OK to use.
· Good listener: Understand the customer's feedback, descriptions, and criticisms. Utilize this information to provide confidence and support for corrective and preventive actions.
· Separate negative feedback from emotions: Collect and review data, provide solutions, and act objectively while supporting the customer's needs.
· Integrity – Do not make something sound good or bad when it isn't. Avoid injecting intuition and hunch into problem solving. If there is a hunch, prove it with data before acting on it. Decisions should not be made based on hunches, anecdotal information, or feelings. Facts and objectivity should guide the risk-based decision making process.
Required Travel: Up to 10%
Education & Experience:
· Bachelor of Science in Engineering
· Experience in a manufacturing environment that includes forming metal and plastics (non-assembly-based operations)
· Experience in automotive industry is preferred – this is preferred so that the sense of urgency and sense of financial impact to organization is understood when receiving a customer concern.