- Direct daily operations of department, analyzing workflow, establishing priorities, developing standards, and setting deadlines.
- Manage and maintain all Quality Control documentation.
- Manage all Quality Control activities as necessary.
- Interface with quality personnel at customer and supplier levels
- Prepare for and manage quality audits, including maintaining Quality Manual and Quality Procedure manual, creating Management review, etc.
- Communicate with external quality assurance officers during on-site inspections.
- Appraise customers' requirements and make sure they are satisfied.
- Perform Sales Order review, Purchase Order reviews, QA clauses, terms & conditions, special notes, specification reviews, etc.
- Participate in product design reviews to provide input on functional requirements, product designs, schedules, or potential problems.
- Develop documentation needed to support testing procedures, including data record forms, equipment logbooks, or inventory forms for New Product Introduction
- Develop and conduct computational analysis for internal and external validation testing as necessary.
- Complete documentation needed to support testing procedures, including data record forms, equipment logbooks, and inventory forms, to ensure replicability and compliance with standards.
- Perform training as necessary in manufacturing.
- Manage customer returns.
- Perform internally driven and customer-driven Root Cause Corrective Actions and failure analysis.
- Maintain and control drawings and specifications.
- Calibrate, validate, or maintain quality control equipment as necessary.
- Maintain training and skills matrix for direct labor and management.
- Create Supplier Corrective Action Request, submit to supplier, and assess SCAR response as necessary.
- Assess discrepant material, create Discrepant Material Request, and notify Material Review Board for disposition as necessary.
- Identify root causes and applicable corrective actions related to quality issues.
- Execute quality control protocols and provide feedback to management for potential improvements.
- Provide support to other engineering areas of operation.
- Read blueprints, data, manuals, or other materials to determine specifications, inspection and testing procedures, adjustment methods, certification processes, formulas, or measuring instruments required.
- Inspect, test, or measure materials, products, installations, or work for conformance to specifications, using measuring instruments such as rulers, calipers, gauges, or micrometers, as necessary.
- Perform visual inspections of finished products and grade, classify, or sort products according to sizes, weights, colors, or other specifications as necessary.
- Conduct routine and non-routine analyses of in-process materials, raw materials, conditioning samples, finished goods, or stability samples as necessary.
- Record inspection or test data, such as weights, temperatures, grades, or moisture content, and quantities inspected or graded as necessary.
- Interpret test results, compare them to established specifications and control limits, and make recommendations on appropriateness of data for release.
- Notify supervisors or other personnel of production problems.
- Any additional tasks necessary to execute on the teams strategy for operational sustainability, improvement, and optimization.
- Bachelor of Science in engineering or related field
- 7-10 years of previous quality or manufacturing experience
- Knowledge of ISO 9001 standards
- Knowledge of AS9100 standards (preferred)
- Ability to read drawings, specifications, acceptance test procedures, etc.
- Proficient in MS Office
- Strong oral and written communication and presentation skills (technical and nontechnical concepts)
- Excellent leadership skills
- Excellent organizational skills
- Results-oriented with strong analytical skills
- Ability to work well independently and part of a team
- Ability to work effectively under stressful and dynamic environments
- Ability to motivate team members in a creative and effective manner
- 401(k)
- 401(k)
- Dental insurance
- Employee assistance program
- Health insurance
- Life insurance
- Paid time off
- Vision insurance
- 8 hour shift
- Monday to Friday
Quality Manager - Bohemia, United States - Power Connector Inc
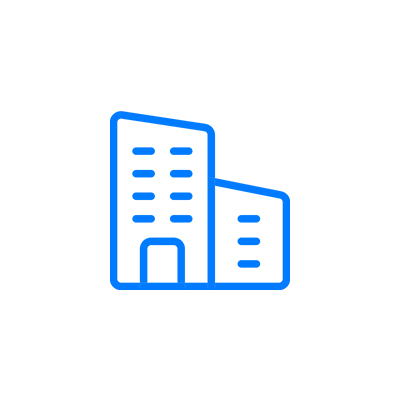
1 month ago

Description
*Job DescriptionQuality Manager
*FLSA Status*: Salary/Exempt
*Reports To*: General Manager
*Direct Reports*: (1) Quality Engineer, (2) Quality Control Inspectors
*Summary
Power Connector, LLC is entering a new and exciting phase of growth and opportunity filled with innovative and progressive thinking and strategizing.
With this historic transition comes the need to enhance and grow the company through restructuring, reorganization, modernization, optimization, and business development.
We, at Power Connector, are responsible for revolutionizing the company and securing and expanding its global connection.Power Connectors Quality Manager is critical in contributing to the fundamental changes that are transforming Power Connector.
This position is instrumental in managing, enhancing, and strengthening our internal Quality Management System by managing and optimizing our internal and external quality processes, procedures, and documentation.
This positions primary focus is to assist, contribute, and execute the teams strategic plans for Quality Management System stability and improvement.
Power Connectors Quality Manager is a dynamic, adaptable, open-minded problem solver with analytical, communication, and management skills suited for individual and team contribution.
This position is an integral part in sustaining and improving our quality system for expansion within our current industry and penetration into new industries.
This position enjoys the inherent challenges of improving and stabilizing quality management systems and manufacturing processes in a diverse, dynamic, and growing organization.
This position has a strong influence on the fundamental principles of the deployed quality management system and leads many initiatives related to the enhancement of internal and external manufacturing and quality processes.
*ResponsibilitiesEducation and Experience
Job Type:
Full-time
Pay:
$80, $100,000.00 per year
Benefits:
Schedule:
Work Location:
In person