- Analyze and troubleshoot plant operations (procedures, equipment, and controls) for efficient and reliable operations.
- Repair and/or install various motors, control valves, transmitters, gauges, wiring, switches, and motor control equipment
- Manage and maintain instrument calibration documentation.
- Performs work requiring a thorough knowledge of instrument application, operation and of the electrical and mechanical principles involved in repair, testing and calibration.
- Maintenance and calibration of process instrumentation devices, electrical power distribution and monitoring devices, VFD drives and motor control.
- Performs preventive and predictive maintenance including calibration, using data collectors, testing and diagnostic tools.
- Investigate equipment failures, determine root cause of failure.
- Able to support call out/on call requirements
- Support safety and environmental personnel to ensure the facilities follow all facility emissions permits (air, water, and solid waste) and safety regulations.
- Design, size, select and estimate installation costs for new process equipment associated with plant modifications and improvements.
- Understand and optimize plant control logic, including implementation via the distributed control system.
- Completes routine process surveys on equipment and operations (pressure, temperature, composition) to ensure efficient operations.
- Actively participate in the completion of inspections during plant outages.
- Complete root cause analysis on plant downtime.
- Actively participate in completing all management of change activities and updating and compliance with Process Safety Management (PSM).
- Develop a working level knowledge of all LSB Industries - Pryor operating units while having a detailed understanding of the interaction between the ammonia unit and the interconnected units.
- Develop, maintain, and track project schedules to ensure that a project execution is timely and on budget.
- Coordinate input from PCC operations, maintenance, EH&S to ensure all needs are supported in day-to-day activities and in projects.
- Develop strong working relationships with all facility personnel, subcontractors, and technology suppliers.
- High School Diploma or Equivalent (i.e., GED)
- Prefer 5-10 years of plant experience.
- Background experience in pneumatic, electro-pneumatic, electronic control loops, motor control circuits, low power distribution and working knowledge of high-voltage sub-stations.
- A minimum of 2 years' experience is desired in installation, troubleshooting, repair of instrumentation and electrical control loops, rebuilding and repair of control valves, electrical motor contactors, replacement of bearings in motors, assisting mechanical group in removal and installation of motors pumps and other electro-mechanical devices.
- Experience and knowledge of HVAC a plus, but not required.
- NFPA 70 arc flash electrical safety.
- Primary duties accomplished by walking/touring safe areas of chemical plant processes. Additional requirements include gaining access to piping, vessels, and tanks both internally and internally and externally using ladders, man-lifts, cranes, and other means as required.
- While performing job duties, the employee frequently works near moving mechanical parts, and in outside weather conditions and is frequently exposed to wet and/or humid conditions.
- The employee may occasionally work in close proximity to chemical processes with toxic or caustic chemicals, airborne particles, fumes, extreme heat, extreme cold, vibration, and electrical hazards.
- Flame-Resistant (FR) uniform, Personal Protective Equipment (PPE) including hard hat, safety glasses, gloves, steel-toed boots, hearing protection, fall protection harnesses, chemical exposure suits are required in designated areas as well as a full-face respirator as necessary in emergencies.
E&I Technician - Pryor, United States - LSB Industris, Inc.
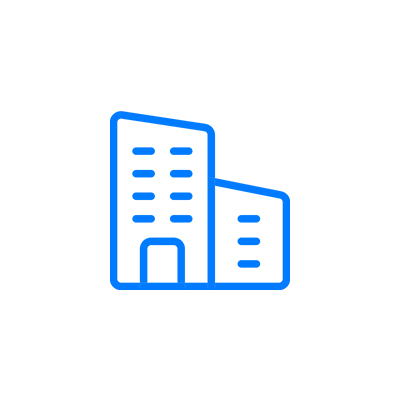
1 month ago

Description
About LSB Industries, Inc.We are a leading North American producer of industrial and agricultural chemicals.
Our vision is to be a "best-in-class", diversified chemical and clean energy producer that safely and efficiently operates our facilities, creates partnerships that deliver value to our customers, suppliers, and logistics providers, and attracts, retains, and enhances the lives of talented team members.
We are well positioned to play a critical role in the reduction of global carbon emissions through our potential to produce low carbon or no carbon ammonia.
We expect our success in achieving these goals to lead to superior financial performance and greater value for our public shareholders.
For more information, view our website atWhy Pryor, OK?
Set against the backdrop of a welcoming small-town atmosphere, Pryor offers an exceptional quality of life with its tight-knit community, excellent schools, and abundance of outdoor activities.
Plus, its proximity to the vibrant city of Tulsa adds an extra layer of excitement, making Pryor the ideal place to both advance your career and enjoy a fulfilling lifestyle.
Join us in this dynamic city and be part of a community that values progress, resilience, and collective success.If you're ready to embark on an exciting career journey filled with purpose, growth, and fulfillment, LSB Industries welcomes you with open arms.
Come to Pryor, OK, and let's transform chemistry into opportunity together. Join us, and let's create a future where every bond we forge is built to last.
The Electrical and Instrumentation (E&I) Technician will provide technical support, installation, and repair services to the operation of all plants with the goal of assisting in the optimization, production, efficiency, and reliability of the units while maintaining a safe plant operation.
Key Responsibilities:
Special Attention:
The position is safety and security in nature.
This position deals with hazardous materials and/or industrial processes that can pose a risk to employees and the general public.
LSB Industries is an equal opportunity employer. In accordance with anti-discrimination law, it is the purpose of this policy to effectuate these principles and mandates.
LSB Industries prohibits discrimination and harassment of any type and affords equal employment opportunities to employees and applicants without regard to race, color, religion, sex, sexual orientation, gender identity or expression, pregnancy, age, national origin, disability status, genetic information, protected veteran status, or any other characteristic protected by law.
LSB Industries conforms to the spirit as well as to the letter of all applicable laws and regulations.