- Bachelors Degree (BSc preferred) or related field
- 4 years of quality related experience minimum.
- IATF 16949/ ISO 9001:2015
- IAG Core tools (MSA/ PPAP/ APQP/ SPC/ AMEF) + CP
- GEMBA Walks, Cross functional process mapping or SIPOC
- Problem Solving methodology 8Ds / PDCA/ Kaizen / DMAIC/ FTA)
- 7 Quality Basic Tools (Pareto diagram/ Scatter diagram/ Histogram/ Ishikawa or fish bone diagram/ Run chart/ Data stratification).
- Internal Auditor
- Basic concepts of Hot Stamping
- Basic concepts of Welding and assembly.
- Six sigma GB or BB/ Red-X/ New science of fixing things.
- Lead Auditor.
- Experience on Stamping process or related.
- Experience on applicable standards on steels.
- CQI-15 (Especial process assessment of welding) or equivalent.
- VDA 6.3
- Plan and conduct the analysis, inspection, design, test, and/or integration of production blanking, laser welding, and mig/tig weld processes to ensure product quality.
- Communicate with the customer.
- Prepare FMEA, Control Plan, and PPAP submissions and approval.
- Train personnel in the use of procedures, work instructions and product acceptance standards.
- Ensure that plant documents requiring controls are identified and properly introduced into the system as well as audits of the quality systems ensuring currency at each location. Maintain an effective current document matrix.
- Audit the quality system and documents obtained during quality assurance activities through the use of statistical process control (SPC) methods.
- Evaluate the need for gauge templates and institute them as needed.
- Use lab equipment as necessary.
- Communicate significant issues or developments to management and recommend corrective/preventative actions.
- Support to achieve all customer targets for PPM and customer complaints. Target is single digit PPMs.
- Support successful launch of all new programs.
- Help drive the LCCS methodology throughout all operations to ensure achievement of all productivity targets.
- Other duties may be assigned.
- Must be able to professionally lead and influence peers.
- Ability to communicate effectively both orally and in writing.
- Understanding of Shiloh quality systems,
- Certified internal auditor for quality systems.
- Strong problem solving skills with ability to lead a team through the process.
- Microsoft Office, PLEX, GAGEpack.
- Ability to define problems, collect data, establish facts, and draw valid conclusions
- Proficient in gage calibrations and MSA requirements
- American Society for Quality certification (CQE, CQA, CQM or CMI and CQT) preferred.
- Occasionally required to walk
- Time split between plant and office environment
- Moderate noise level in the plant
- This position will perform work in both the plant and office environment with unrestricted movement
- Some travel as required
Quality Engineer - Goshen, United States - Dura-Shiloh
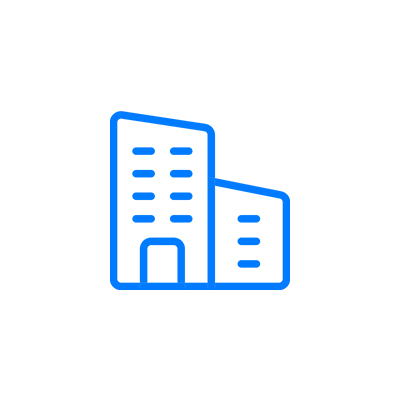
1 month ago

Description
Summary:
The Quality Engineer is responsible to evaluate and improve product quality and the quality system. The Quality Engineer assists in monitoring and improving the effectiveness of the quality system and controls.
Education and/or Experience
Essential Knowledge:
Desired Knowledge:
Duties and Responsibilities; included but are not limited to:
Supervisory Responsibilities
Skills and Abilities
Certificates, Licenses, and Registrations
Additional Competencies
Physical Demands
Work Environment
Reasonable accommodations may be made to enable individuals with disabilities to perform the essential functions of this position.
This job description will be reviewed periodically as duties and responsibilities change with business necessity. All job functions are subject to modification.