No more applications are being accepted for this job
Quality Manager - Beasley, United States - Mariden Search
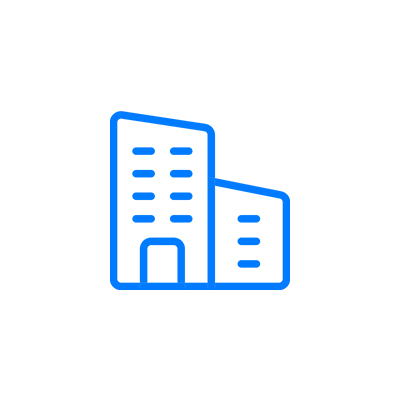
Mariden Search
Beasley, United States
1 week ago

Description
Job DescriptionJob Description
Our client is building a new Quality and Safety team to upgrade their standards in the industry.
At their facility in Beasley, TX they manufacture air cooled heat exchangers and axial flow fans.
The site is approximately 120 acres and has 466 employees.
TheQA/QC Manager is a hands-on working manager who works with minimal supervision to establish and uphold quality systems and processes.
expectations.
Measures
and reports on performance and trends in product quality and takes the lead in continuous
improvement.
Analyzes
quality issues, non-conformances, root cause analysis, and documents all corrective and preventive actions.
Leads by example to establish a customer focused (internal and external) Quality Team.
What Your Day-to-Day Activities Will Be
Maintains HPCs ASME and NB Code
Stamps/Certifications
Maintains HPCs CWB (Canadian Welding Bureau) Certification and coordinates inspections for HPM.
Be the Subject Matter Expert for Quality topics for Hudson Products Corporation
Manages the conduction of Internal Audits to ensure conformance to required QMS
Familiar with basic metallurgical concepts such as heat treat methods, material grades and chemistries, manufacturing processes, NDT methods
Leads and manages customer quality audits.
Ability to build and strengthen existing QMS.
Manages QA/QC Team to ensure production needs are met while ensuring product quality
Works with Purchasing Team to establish and maintain Vendor product quality including site audits and qualification reviews for new vendors
Your Education Should Be
Minimum Education:
Bachelors degree in engineering or a Technical field
Minimum Experience:
10 years in a Quality role
5 years of management experience
Your Physical Work Environment Will Require
Mostly Outdoor/Shop Environment
Some Indoor/Office Environment
Some Noisy/Loud Shop Environment
Safety Glasses
Steel Toe Shoes
Hardhat (in required areas)
Safety Vest
Ear Plugs
Gloves (when needed)
Face Shield (when needed)
Your Professional Experience Should Be
Works with vendors to provide resources for NDT testing on-site and laboratory testing of weld mockup/welder test samples (assist Welding Engineer)
Maintains Calibration of all required HPC instrumentation
Plan, promote, and organize training activities related to product quality and reliability
Owns NCR Process and Leads Analysis of Quality and Production Process Issues and Non-Conformances to provide Corrective Action/Preventive Action
Works with Operations to inspect work in-process to improve overall productivity and minimize costs associated with Non-Conforming Parts/Materials.
Establishes Quality Metrics including reporting and continuous improvement initiatives to improve metrics.
QITPs (Quality Inspection Test Plans) and NDE plans for each customer order
Product Testing NDE, Leak, Pressure, Noise, Weld Mockups, etc.
Maintains all relevant Quality Data and generates Quality Data Books for all Customer Orders
Investigates Customer Complaints and takes Corrective Action when needed while providing detailed reporting of the incident to Project Management.
Establishes Goals for Quality Team in support of HPC initiatives.
Weekly reporting.
Approx Comp $120k-$130k plus 20% STI
#J-18808-Ljbffr