- In coordination with Senior Director of Quality, develops and executes quality and regulatory strategies and systems to comply with Quality System Regulations (QSR), Medical Device Directive (MDD), International Standards Organization (ISO), Recognized Consensus Standards and all other applicable quality system requirements. Ensures compliance to 21 CFR Part 820, 21 CFR Part 211, 21 CFR Part 4, ISO 13485, MDR 2017/745, UK MDR 2002, other regulatory requirements, company policies, operating procedures, processes, and task assignments.
- Manages and maintains the effectiveness of the Delcath Quality Management System at the Queensbury sites and manages the resolution of all quality concerns and related issues as required.Acts as the Deputy Management Representative for Queensbury.
- Executes day-to-day processes for medical device manufacturing facility QA accountabilities to ensure continual regulatory compliance with FDA, Outside US Regulatory Authorities, and Notified Body and Approved Body requirements.
- Provides oversight for product releases: finished products, raw materials, packaging components, and labeling.
- Supports the Corrective Action and Preventive Action Program.
- Supports the Internal Audit Program through the performance of audits as required.
- Supports the Supplier Quality Program and perform on-site quality audits, as required.
- Supports Customer Complaint investigations.Ensure Customer Complaint records are properly maintained, followed-up, and closed.
- Supports the Routine Metric Review and the Management Review process to monitor and evaluate Quality System effectiveness.
- Maintains current knowledge base of all regulatory and quality assurance related changes within the industry.
- Provides Quality leadership to development teams.Represents the Quality discipline by providing support to all Sustaining Engineering Projects.
- Works closely with internal regulatory staff and external consultants to prepare, review medical device manufacturing documentation for domestic and international paper-based and electronic regulatory submissions.
- Collaborates with the Regulatory Team to recommend and implement regulatory strategies for product line extensions in support of product development team efforts and provide guidance to those teams to ensure that development activities are consistent with overall regulatory strategy.
- Reviews and interprets technical and scientific data to ensure regulatory requirements are met; evaluates product/design and process changes for potential effect upon product safety and effectiveness; appropriately document Quality disposition of such changes.
- Reviews and maintains Quality Systems programs to ensure continuous improvement and regulatory compliance.
Senior Quality Assurance Manager - Queensbury, United States - Delcath
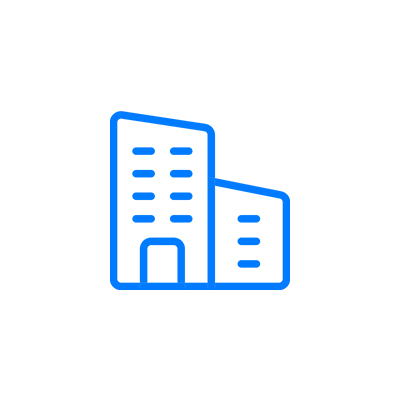
1 month ago

Description
POSITION SUMMARY
Responsible for ensuring the effective establishment and maintenance of the Delcath Quality System and ensuring that the facility is fully compliant to all applicable national and international regulations and standards.
Responsible for Quality oversite of the day-to-day medical device manufacturing activities including supplier control oversite, incoming and in-process quality inspection, NCR/CAPA/Complaint review approval and product release.Provides direct tactical Quality support for multiple projects within Delcath Systems, Inc. to provide execution of the development, launch and post-approval maintenance of medical device components and finished medical devices according to the approved Design Control procedures.
This position retains signatory authority for Quality Management.
ESSENTIAL DUTIES AND RESPONSIBILITIES include the following.Other duties may be assigned.
EDUCATION and/or EXPERIENCE
A minimum of Bachelors degree in engineering or physical sciences.
A minimum of five or more yearsof experience in quality assurance, quality engineering, or related functions in a FDA regulated industry or ISO certified organization is required. In addition, a minimum of three or more years' experience as a direct supervisor/manager of Quality Professionals.
Must be team oriented, with the ability collaborate with diverse cross-functional teams.
Must possess strong analytical and process skills, and be computer proficient in Minitab, EXCEL, Word, etc.
Must possess strong verbal and written communication skills.
Must be an effective leader of the Quality team to ensure goals are established and monitored and must provide input and direction to team members to ensure issues are addressed in a timely manner and project status is communicated across the organization.