Manufacturing Engineering Manager - West Columbia, United States - Philips Recruiting Services / Philips Automotive Recruiting
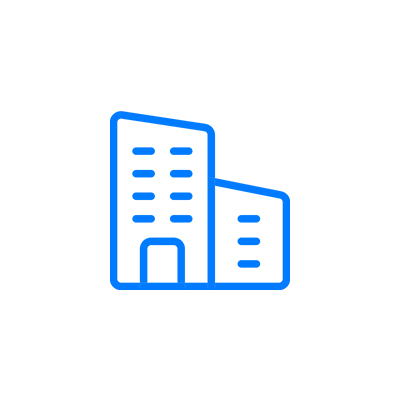
2 weeks ago

Description
MANUFACTURING ENGINEERING MANAGER**Candidates must have experience and demonstrated success in complex AUTOMOTIVE operations.'The Engineering Manager is responsible for planning, directing, and coordinating activities of designated projects to ensure that goals or objectives or projects are accomplished within prescribed time frame and funding parameters by performing the following duties personally or through subordinate supervisors; this will include and is not limited to calling and running internal and external team project review meetings, writing and maintaining and certain portions of program books, facilitating customer communication, maintaining and publishing open issues, developing and tracking project timing, provide the first level of resolution or inter-project differences and problems affecting project execution and communication.
Essential Duties & Responsibilities:
Review project proposal or plant to determine time frame, funding limitations, procedures for accomplishing project, staffing requirements and allotment of available resources to various phases of project.
Makes customer presentations relating to timing and product performance and assures that Customer interaction is occurring on a regular basis in these areasDirect plant engineering activities.
Monitor new product introduction activities. Manage efforts related to VA/VE initiative.Confers with project personnel to provide technical advice and to resolve problems.
Set up and maintain productions tooling and equipmentParticipate in objective setting, plan development and performance review of plant performance.
Initiates, implements, and manages the plant maintenance program based on best practices in the Automotive planning/scheduling and preventive/predictive maintenance.
Monitors the use and inventories of spare parts, maintenance supplies, and equipment and initiates reordering when necessaryEstablishes and maintains a computerized maintenance management system (CMMS) for tracking work orders, spare parts, and maintenance history of plant equipment.
Prepares reports, analyzes data, and makes recommendations for improving plant operations and solving maintenance-related problemsEnsures that maintenance technicians are adequately trained, equipped, and motivated so that the maintenance program can be accomplished in a safe, timely, and cost-effective manner.
Reviews the operation of plant equipment and systems constantly, to minimize unplanned downtime, anticipate solve problems in a timely manner, and to identify opportunities for improvement.
Maintains and updates operating and training manuals for the maintenance department.Ensures that all maintenance technicians are trained on the most updated technology and operating procedures.
Reviews the operation of plant equipment and systems constantly, to minimize unplanned downtime, anticipate solve problems in a timely manner, and to identify opportunities for improvement.
Plans the performance of preventative maintenance activities based upon personal knowledge and interval records of equipment wear and the manufacturers recommendations regarding service.
Schedules and coordinates the accomplishment of this work to minimize interference with production operations.Develops and maintains key, preferred suppliers and spare part inventories. Schedules incoming materials for planned maintenance activities.
Schedules work to prevent idle time and to provide maximum machine utilization. Schedules overtime work among maintenance employees to equalize overtime fairly. Determines priority of maintenance job backlog and schedules work accomplished. Schedules vacations in such a manner to not interfere with necessary maintenance.
Responsible for up-grading the effectiveness of maintenance personnel. Schedules and conducts meetings with instructions relating to maintenance skills, safety, and Company Policy.
Handles all job-related problems in maintenance honestly and fairly without violation of Company Policies or Procedures.
Actively participates in Health/Safety/Environmental investigations and the 8D process in order to develop root cause analysis for problem resolution as required.
Ensure required Safety Audits are complete for you and your team.Reporting accidents, occupational illnesses, and HSE&E emergencies, and inform supervisor of known HSE&E conditions which could adversely affect other team members, assets or to the public.
Ensures compliance with all safety procedures and ensures safe working procedures in assigned production areas.Participates in or assigns team members to participate in Job Safety AnalysisAssist the plant in achieving safety goals and achieving and maintaining JCMS objectives.
Performs other duties deemed necessary by the Plant Manager.Has the authority to stop the production process if a quality or safety concern is noticed.
Qualification Requirements:
To perform this job successfully, an individual must be able to perform each essential duty satisfactorily. The requirements listed below are representative of the knowledge, skill, and/or ability required. Reasonable accommodations may be made to enable individuals with disabilities to perform the essential functions.
Education & ExperienceBachelors Degree or other Technical degree, and/or one (1) to two (2) years related experience and/or training in a Manufacturing Environment.
Four (4) plus years of managerial experience#J-18808-Ljbffr