- Establish a business relationship with customer(s) and provide exceptional
- Provide and maintain Quality Control Plans for all assigned products
- Work independently or in a team to develop and implement solutions to quality
- Be an integral part of the company-wide effort of Built In Quality (BIQ).
- Identify and document the dimensional and appearance Key Characteristics (KC)
- Work with engineering in the development of gauges and fixtures to control
- Assist operations in the training of employees in the use of all gauging and
- Collect product quality data and maintain charts on Key Performance Indicators
- Regularly post KPIs on communication boards in the operating areas, including
- Work with engineering and operations personnel to drive quality defects back to
- Participate in scheduled CQAs and communicate findings back to the operations
- Participate in MRBs and in determining disposition of NCM.
- Request, review, and approve supplier PPAPs.
- Support the completion of all requested forms in support of customer PPAPs,
- Submit and track customer 8D reports.
- Serve as escalation step for supplier non-conformances.
- Participate in the AQP Process, ensuring plant readiness for product and process
- Frequent communications and visits with customer to support a partnership
- Conduct and/or participate in supplier development activities for key suppliers
- Quality improvement programs that target DPPM
- Provide current, accurate quality performance metrics to operations
- Coaching and developing inspectors
- Setting performance improvement goals for the KPIs
Quality Enginner - Anderson, United States - McLaughlin Body Company, Inc.
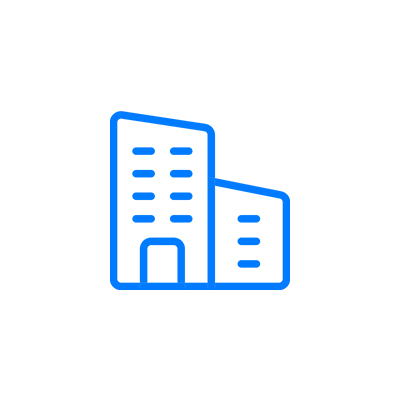
McLaughlin Body Company, Inc.
Anderson, United States
1 week ago

Description
Job Description
Job DescriptionObjectives:
Duties:
identified by MBC.
PPM (DPPM).
Dimensional Results, Balloon Diagrams, Part Submission Warrants, Process Flow
Diagrams and Process FMEAs.
Responsibilities:
EXPERIENCE:
Requires bachelor's degree in technical
engineering or three to five years of related experience, or a combination of education
and related experience.