No more applications are being accepted for this job
- Be the champion of a strong culture of high quality and be the main point of contact for all processes and procedures related to quality
- Act as the Quality Management Representative and manage the ISO 9001 program and ensure compliance with the standard
- Coordinate and facilitate Management Review Committee meetings
- Plan, coordinate, and monitor the internal audit program
- Develop and implement quality assurance policies, procedures, and standards to ensure compliance with industry regulations and customer requirements
- Monitor and analyze key quality metrics to track performance and drive continuous improvement initiatives
- Aid in the pursuit of additional certifications and standards in alignment with company vision and business direction2. Inspection department management
- Manage the Inspection Department personnel and related processes
- Ensure inspection data is properly reported and filed
- Prioritize workflow in the inspection department working closely with manufacturing team members and project engineers3. Process Improvement
- Lead continuous improvement efforts company-wide by collaborating with managers to create efficiency and eliminate waste using tools such as Six Sigma, Lean Manufacturing, and Kaizen.
- Manage the entry, analysis, and application of data in the RADAR lessons learned software system4. Supplier Quality Management
- Collaborate with procurement and supply chain teams to establish quality requirements and monitor performance for suppliers and vendors
- Assist in resolving supplier quality issues including processing Corrective Action Requests5. Customer Satisfaction
- Serve as the primary point of contact for customer quality issues and concerns, ensuring timely resolution and effective communication
- Help analyze risk and confirm that critical characteristics of projects are following specifications
- Lead efforts to ensure final inspections are conducted and equipment is validated prior to shipping6. Training and Development
- Provide training and guidance to employees on quality standards, procedures, and techniques to ensure a culture of quality throughout the organization
- Foster a collaborative environment that promotes continuous learning and development to enhance employee skills and capabilitiesInterpersonal Responsibilities1. Collaborate with team members, motivate and persuade others to do what is needed, exhibit strong team leadership skills. Be a strong influencer.2. Communicate effectively with stakeholders at all levels of the organization, present concepts and expectations clearly in both written and oral formats3. Organize and plan efficiently with strong attention to detail, use systems and tools to analyze data and make sound decisions4.
- Bachelor's degree in Engineering, Quality Management, or similar field
- 5 years' experience in manufacturing with emphasis in Quality Management
- Strong knowledge of Quality principles and methodologies
- Familiarity with Quality Management Systems and standards like ISO 9001, etc.
- Experience in the inspection of precision components and assemblies using a variety of tools and techniques
- Knowledge of CMM and Laser Tracker inspection devices
- Knowledge of statistical process control including Cp and Cpk
- Good working knowledge of GD&T
- Performance and reporting of Gage R&R studies
Quality Manager - Richmond, United States - Ahaus Tool and Engineering
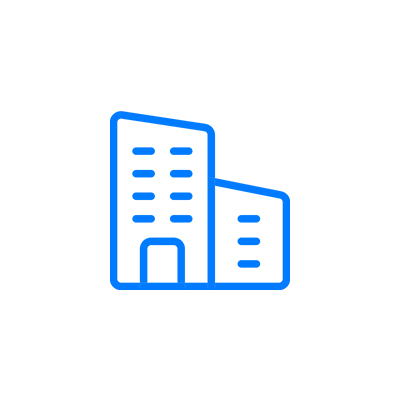
Ahaus Tool and Engineering
Richmond, United States
4 weeks ago

Description
JOB TITLE:
Quality Manager
REPORTS TO:
Vice President
JOB SUMMARY:
The Quality Manager plays a crucial role in ensuring that our products meet the highest standards of quality, reliability, and performance.
They will be responsible for developing and implementing quality assurance policies, procedures, and initiatives to optimize our engineering and manufacturing processes to enhance overall product quality and ensure that our products meet or exceed customer expectations and regulatory requirements.
Key performance objectives in order of priority with ideal time allocation are:1. Quality assurance management (25%)2. Inspection department management (20%)3. Process improvement (20%)4. Supplier quality management (5%)5. Customer Satisfaction (5%)6. Training and development (5%)Note:
Twenty percent of time is reserved for ancillary responsibilities, interruptions and unplanned events
ESSENTIAL DUTIES AND RESPONSIBILITIES:
To perform this job successfully, an individual must be able to perform each essential duty satisfactorily. The requirements listed are representative of the knowledge, skill, or ability required. Other duties may be assigned.
Operational Responsibilities1. Quality Assurance Management
Be Respectful, Be Reliable, Be Collaborative, Be Better5. Be personally accountable, independent, and self-motivatedPreferred Education and Experience