- Process Safety Management (PSM): Ensure strict compliance with PSM regulations and other relevant safety and environmental standards. Oversee the implementation of PSM elements such as Process Hazard Analysis, Mechanical Integrity, and Operating Procedures. Lead incident investigations and ensure corrective actions are implemented.
- Bachelor's degree in Chemical Engineering, Process Engineering, or a related field.
- Minimum of 5 years of experience in a leadership role within a chemical or polymer manufacturing environment.
- Strong knowledge of Process Safety Management (PSM) regulations and experience managing PSM elements.
- Proven track record of improving operational efficiency and safety performance.
- Excellent leadership, communication, and interpersonal skills.
- Ability to work in a fast-paced, high-stress environment.
- Six Sigma or Lean Manufacturing certification is a plus
- This role requires working in an industrial plant environment, including exposure to chemicals, loud noises, and machinery. The Operations Manager may be required to work outside of normal business hours, including nights, weekends, and holidays, to oversee plant operations or respond to emergencies.
-
manufacturing ops mgr
4 days ago
Pure Cycle Ironton, United StatesJob Description · Why PureCycle? Public company - NASDAQ PCT · Industry best PTO plan · Competitive pay structure (includes cash and equity incentives) · Full benefits (Medical, Dental, Vision, 401k) · Awarded "Best Places to Work" two years in a row by Plastics News (2022, 202 ...
manufacturing ops mgr - Ironton, United States - Pure Cycle
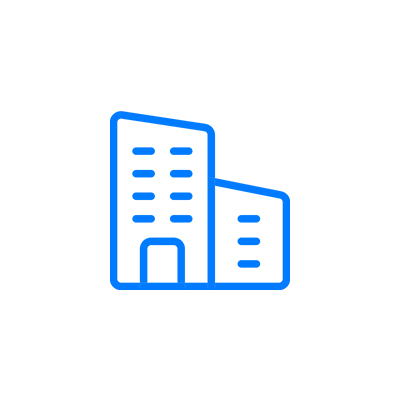
3 weeks ago

Description
Job DescriptionWhy PureCycle? Public company - NASDAQ PCT Industry best PTO plan Competitive pay structure (includes cash and equity incentives) Full benefits (Medical, Dental, Vision, 401k) Awarded "Best Places to Work" two years in a row by Plastics News (2022, 2023) First-of-its-kind manufacturing processes/facilities designed with advanced technology and a "Born Digital" strategyLocation:
Ironton, Ohio - Must be in a commutable distance or willing to relocate
Job Summary:
The Operations Manager is a crucial leadership position within our polymer recycling plant, ensuring operational excellence, safety, and compliance with all Process Safety Management (PSM) regulations.
The Operations Manager is responsible for fostering a culture of safety, efficiency, and continuous improvement, ensuring the plant operates reliably and meets production targets while complying with environmental, health, and safety standards.
Key Responsibilities:
Operational Leadership and Management:
Oversee the plant's daily operations, ensuring efficiency, quality, and safety. Develop and implement operational strategies to meet production targets and objectives.
Mentor and manage a team of shift supervisors, operations specialists, hourly operations staff, and technicians, promoting a culture of teamwork and continuous improvement.
Performance Monitoring and Improvement:
Monitor operational metrics and KPIs, identifying opportunities for performance improvement. Implement lean manufacturing principles and Six Sigma methodologies to enhance operational efficiency and reduce waste.
Training and Development:
Develop and oversee training programs for operations staff, ensuring all team members are proficient in operational procedures, safety protocols, and PSM requirements.
Foster a culture of learning and development.Budget and Cost Control:
Manage the operations budget, including labor, materials, and overhead costs. Implement cost-saving initiatives to optimize operational expenses without compromising safety or quality.
Stakeholder Engagement:
Collaborate with other departments, such as Maintenance, Quality Assurance, EHS and Human Resources, to ensure operational alignment with overall plant objectives.
Act as a key liaison with regulatory bodies, ensuring compliance with all legal and regulatory requirements.Emergency Response and Crisis Management:
Lead the operations team in emergency preparedness and response. Ensure effective crisis management procedures are in place and understood by all operations staff.
Qualifications:
Working Conditions:
About UsWhy PureCycle? Public company - NASDAQ PCT Industry Best PTO Plan Competitive pay structure (includes cash and equity incentives) Full benefits (Medical, Dental, Vision, Retirement plans, 401k) Awarded "Best Places to Work " two years in a row by Plastics News (2022, 2023) Rapidly growing recycling tech start-up company - Building 50 plants in 15 years First-of-its-kind manufacturing processes/facilities designed with advanced technology and a "Born Digital" Strategy PureCycle's mission is to help solve the global environmental problem created by plastic waste.
By diverting #5 plastic away from landfills and oceans, waste plastic can have a new life as a valuable renewable resource.
Through PureCycle's ground-breaking patented recycling process, we separate color, odor, and contaminants from plastic waste to transform it into ultra-pure recycled resin.
We provide our purified polypropylene resin to large companies like Procter & Gamble and L'Oreal to give them a sustainable solution for future products and packaging.